工場進捗状況
Progress
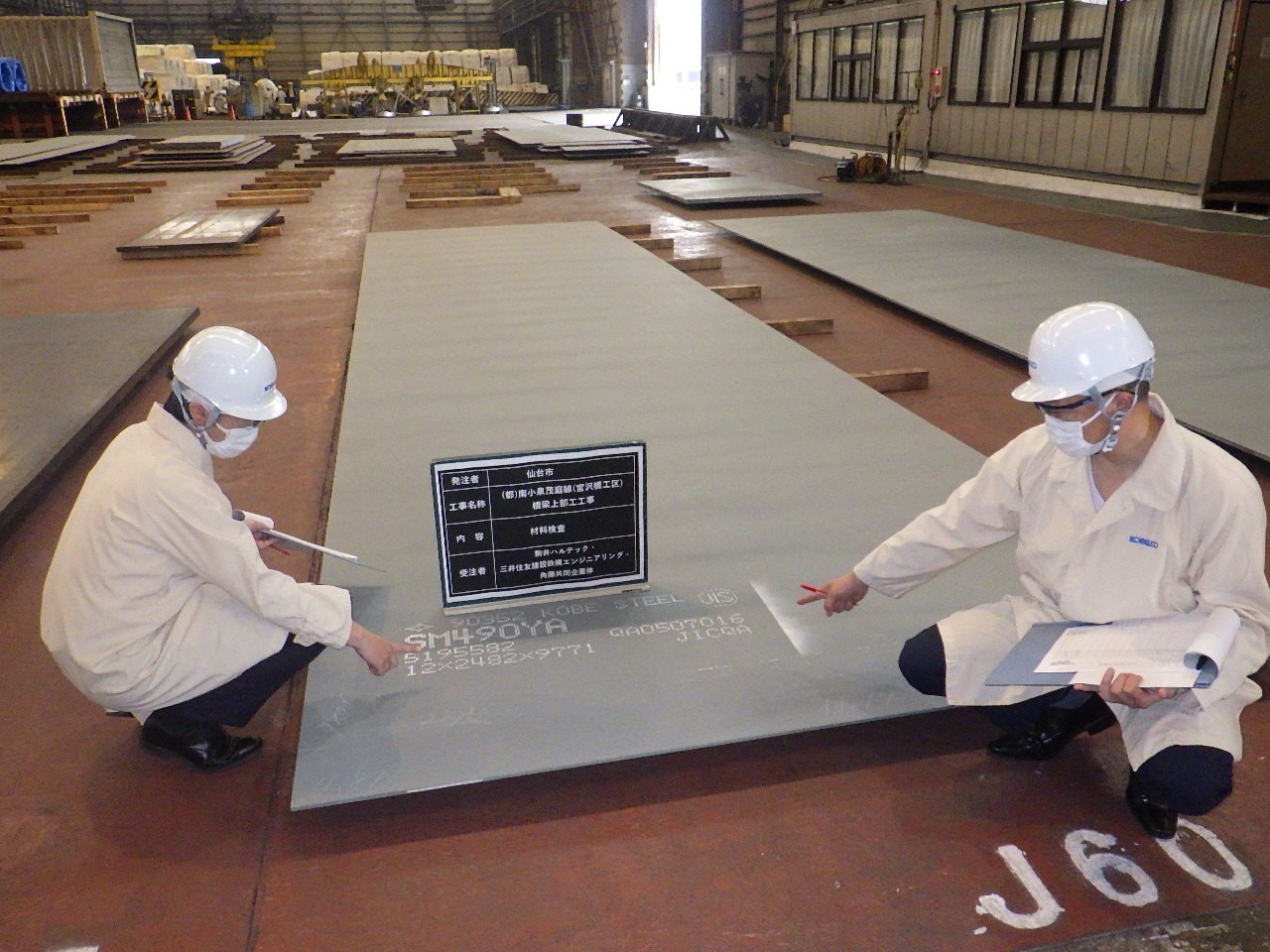
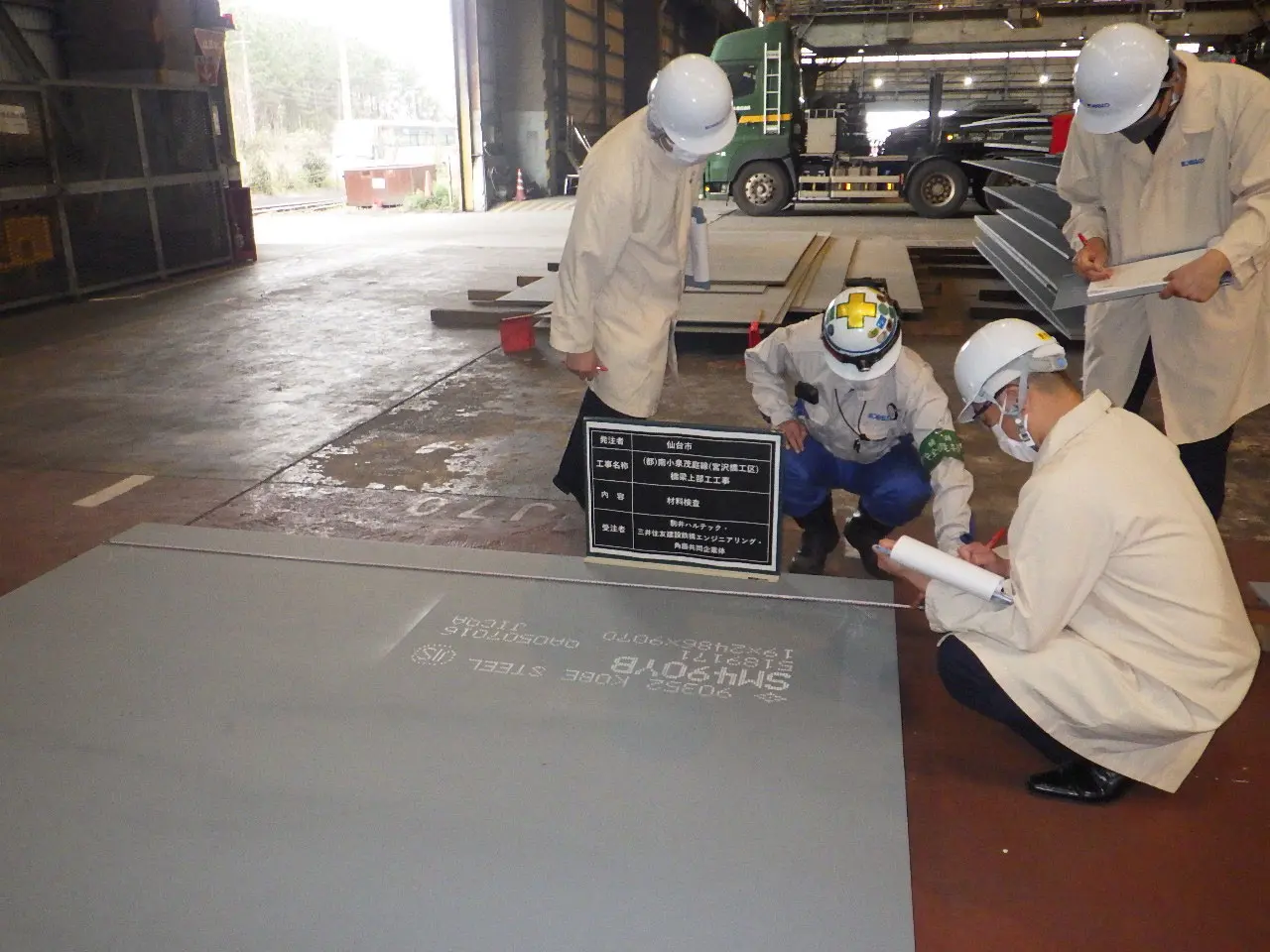
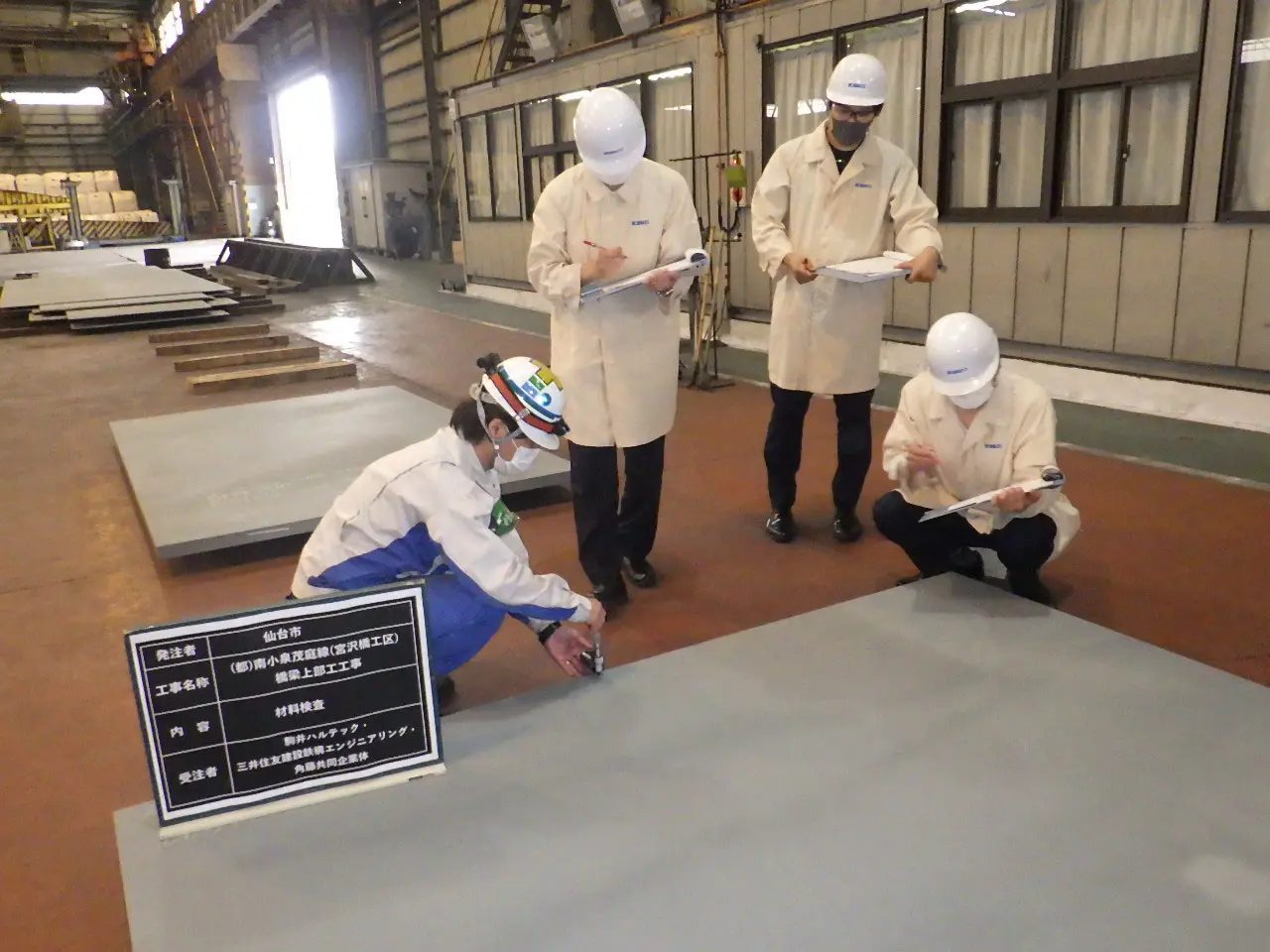
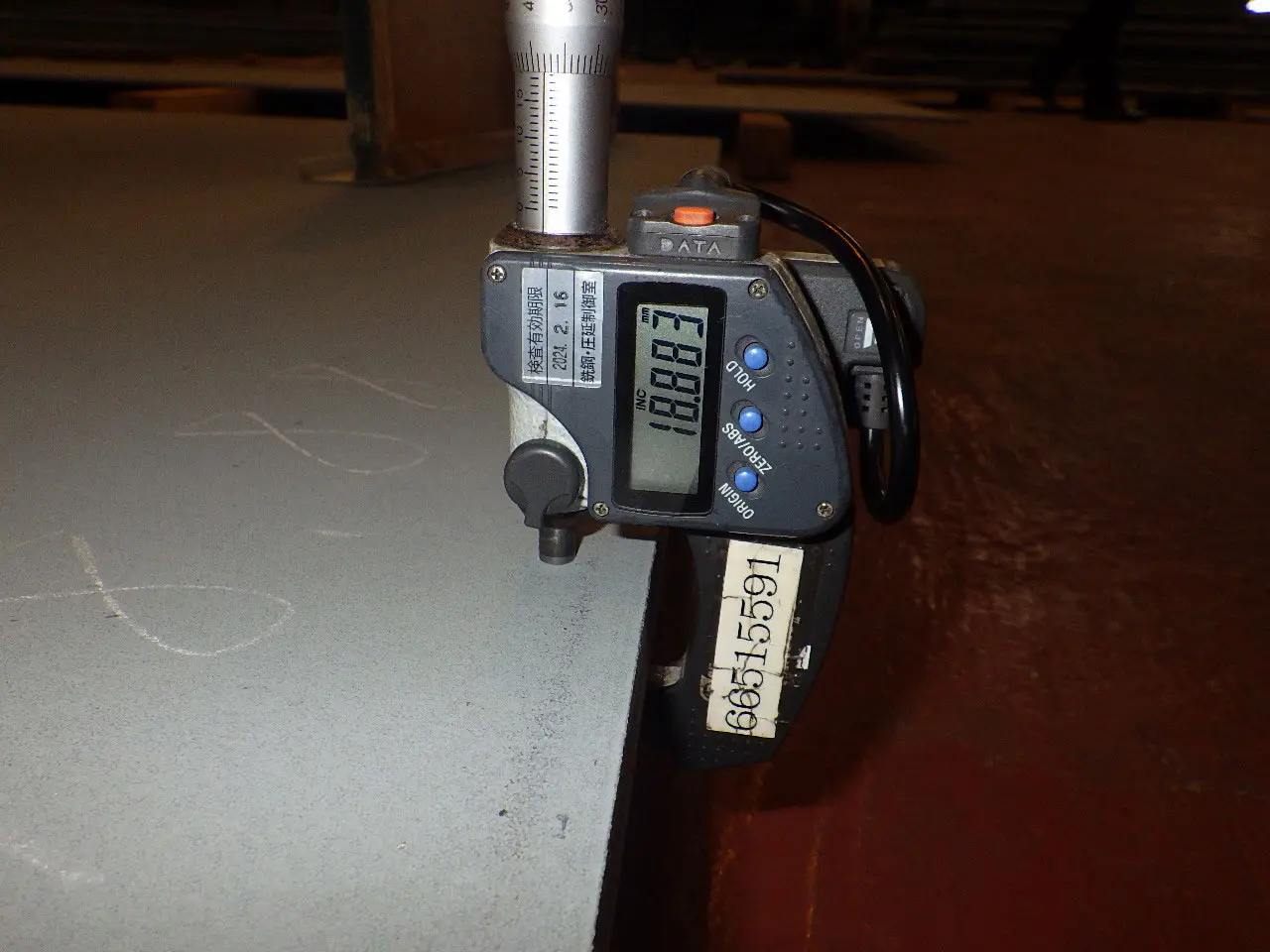
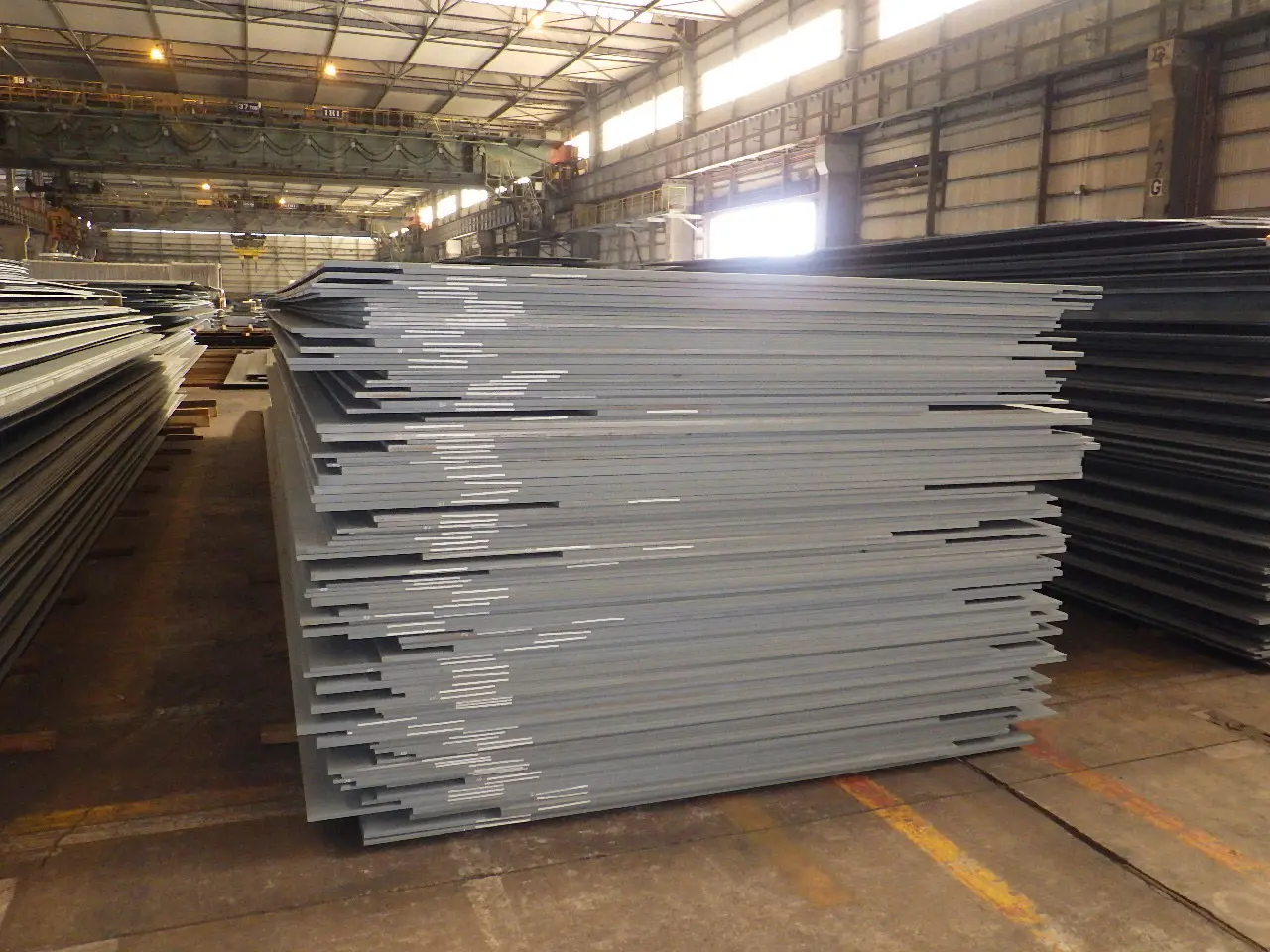
1.鋼板材料検査
鋼橋に用いられる鋼材は、設計図書に記載された鋼材規格に、合格していることを施工着手前に確認する必要があります。使用する全ての鋼材は、ミルシートと呼ばれる、鋼材メーカーより発行される品質証明資料により材料品質の確認を行います。
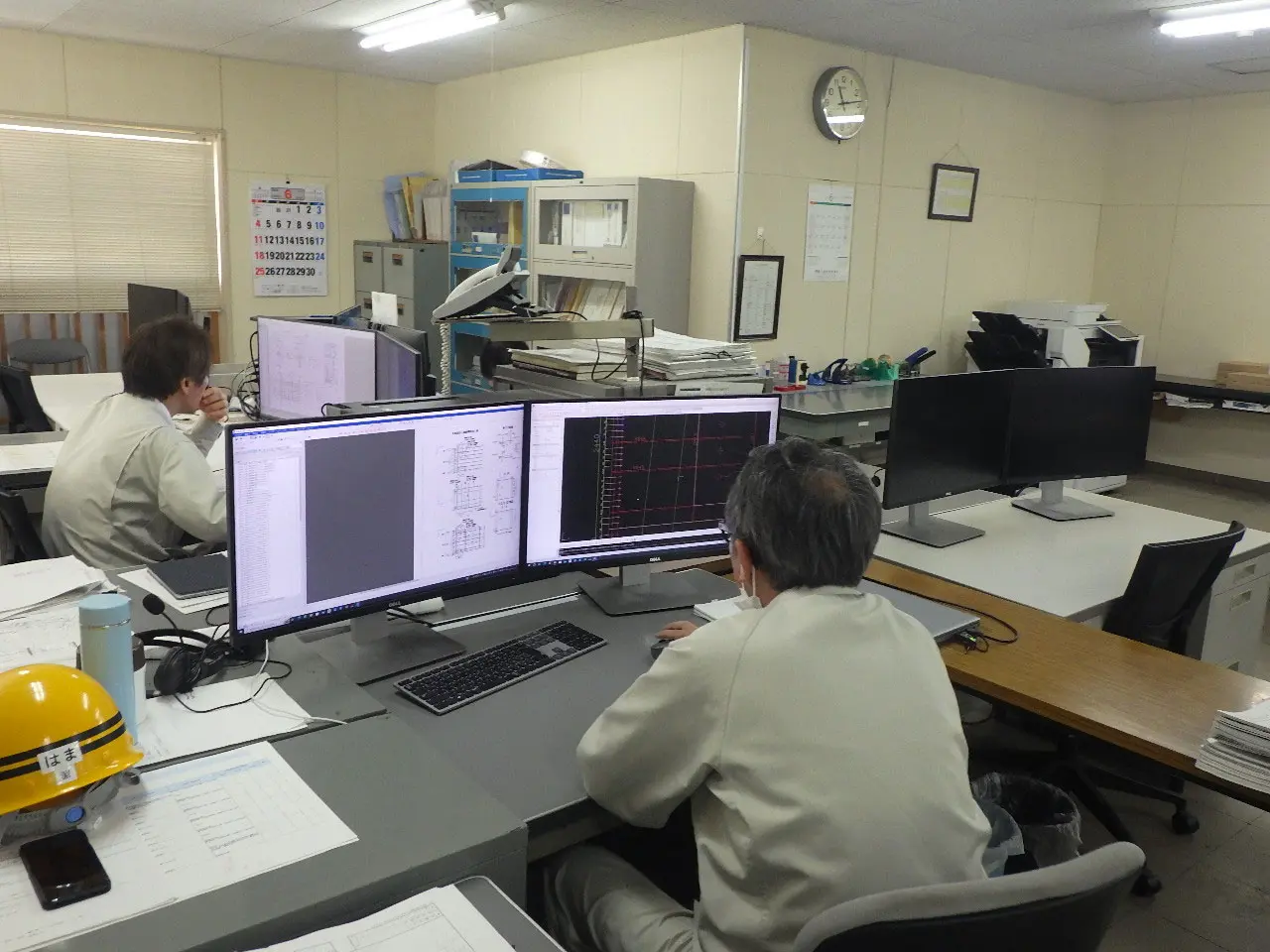
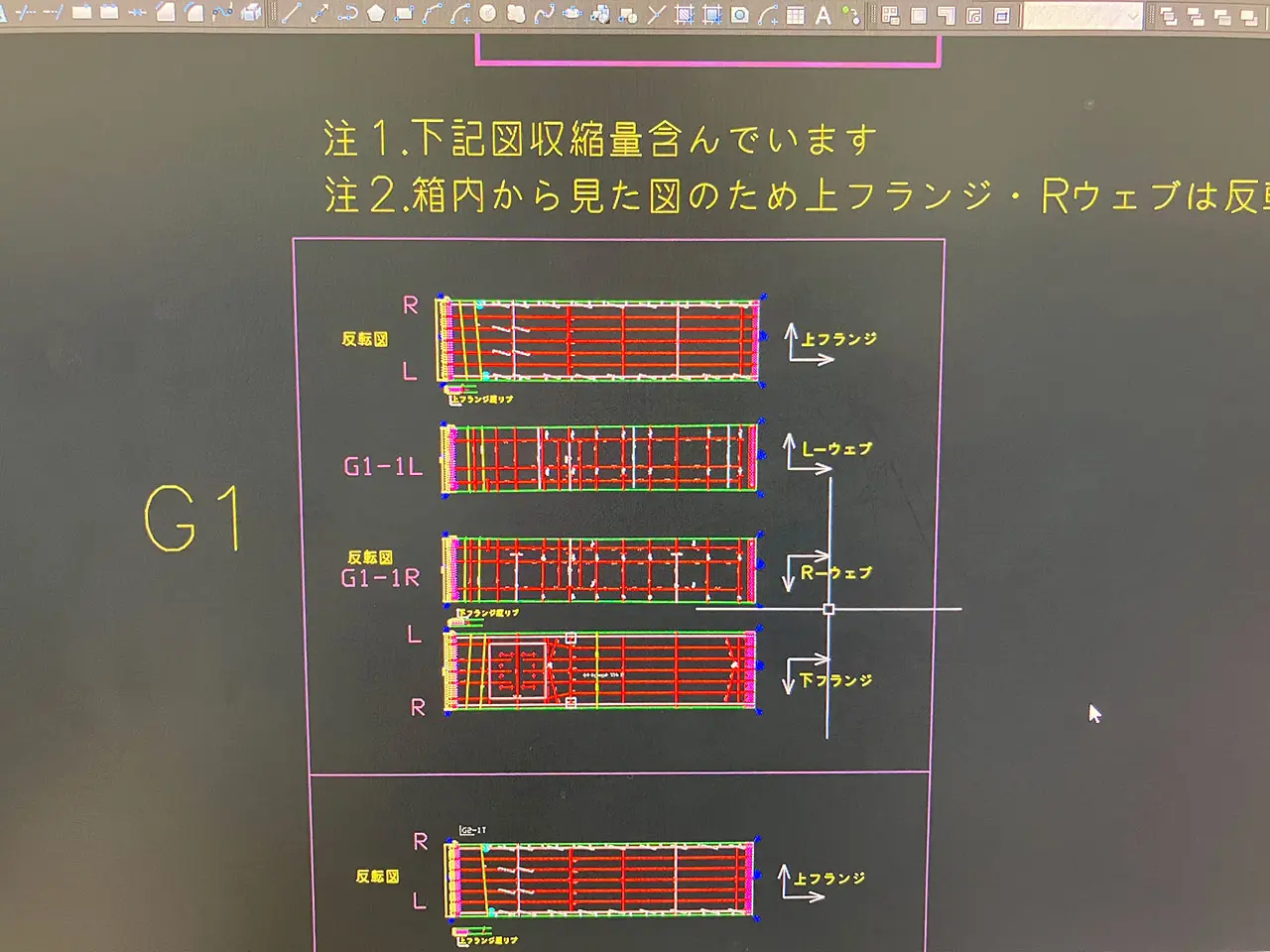
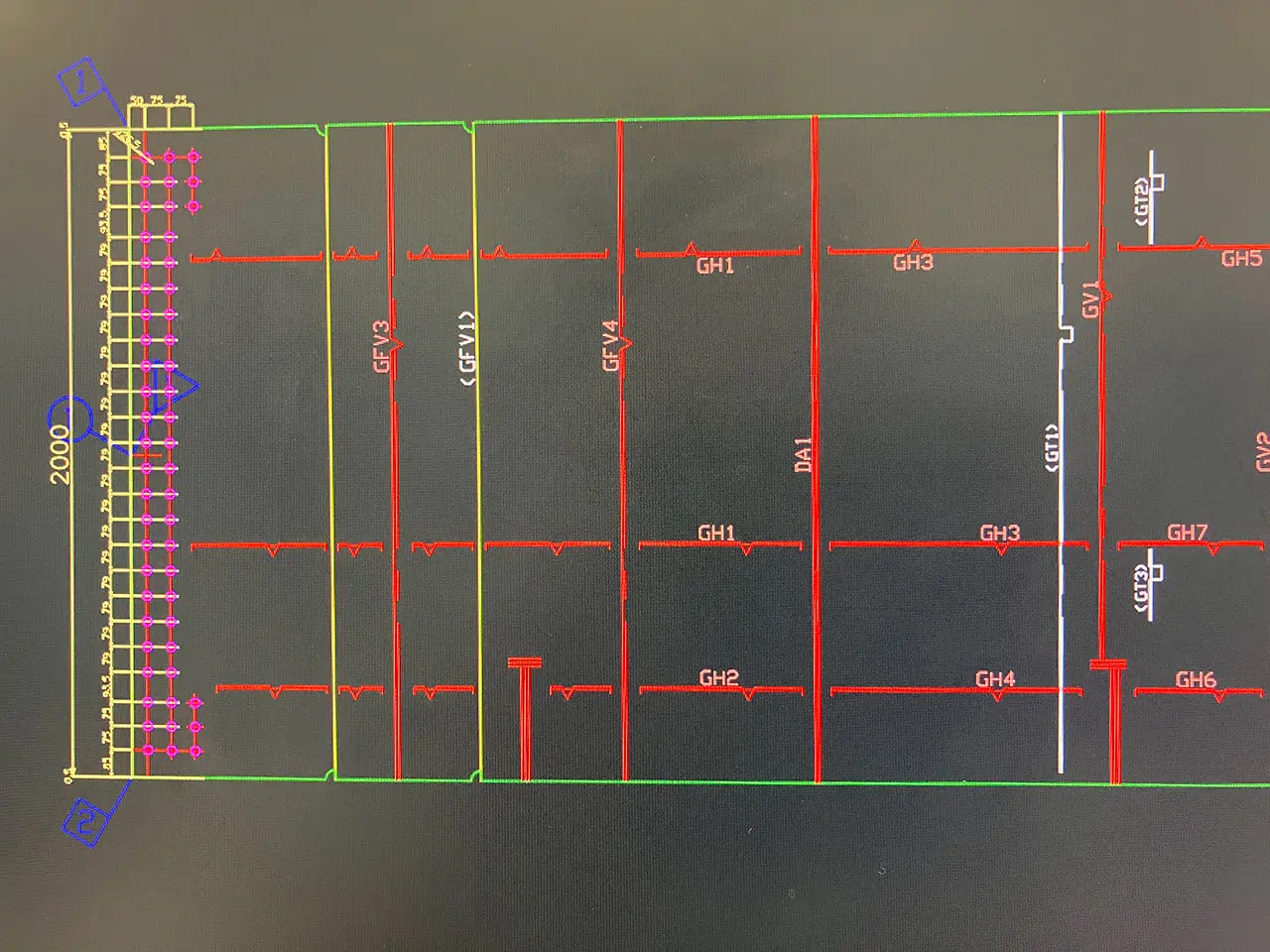
2.原寸作業
原寸作業とは、鋼橋製作における製作情報を作成する作業です。
原寸作業では、主に3つの作業を行います。
一つ目は、『正確な寸法の決定』。設計図面情報の縦断勾配、キャンバー、平面線形等の要素を含み、溶接の収縮や変形を考慮し、実際に加工する部品、部材の正確な寸法を決定します。
2番目は『加工データの作成』。原寸作業で作成したNCデーターと呼ばれる、場内作業の負荷軽減・工程短縮の為に使用する自動機器を動かす為の、座標情報を含んだデータや各種帳票、部材や仮組立等の寸法管理表や架設時の部材マーク図などを作成します。
3番目は『施工上の支障がないかの検討』。各部品・部材の取り合い関係や干渉の有無、工場製作や架設現場での作業時に施工上の支障がないかどうかの確認・検討を行います。
原寸作業では、主に3つの作業を行います。
一つ目は、『正確な寸法の決定』。設計図面情報の縦断勾配、キャンバー、平面線形等の要素を含み、溶接の収縮や変形を考慮し、実際に加工する部品、部材の正確な寸法を決定します。
2番目は『加工データの作成』。原寸作業で作成したNCデーターと呼ばれる、場内作業の負荷軽減・工程短縮の為に使用する自動機器を動かす為の、座標情報を含んだデータや各種帳票、部材や仮組立等の寸法管理表や架設時の部材マーク図などを作成します。
3番目は『施工上の支障がないかの検討』。各部品・部材の取り合い関係や干渉の有無、工場製作や架設現場での作業時に施工上の支障がないかどうかの確認・検討を行います。
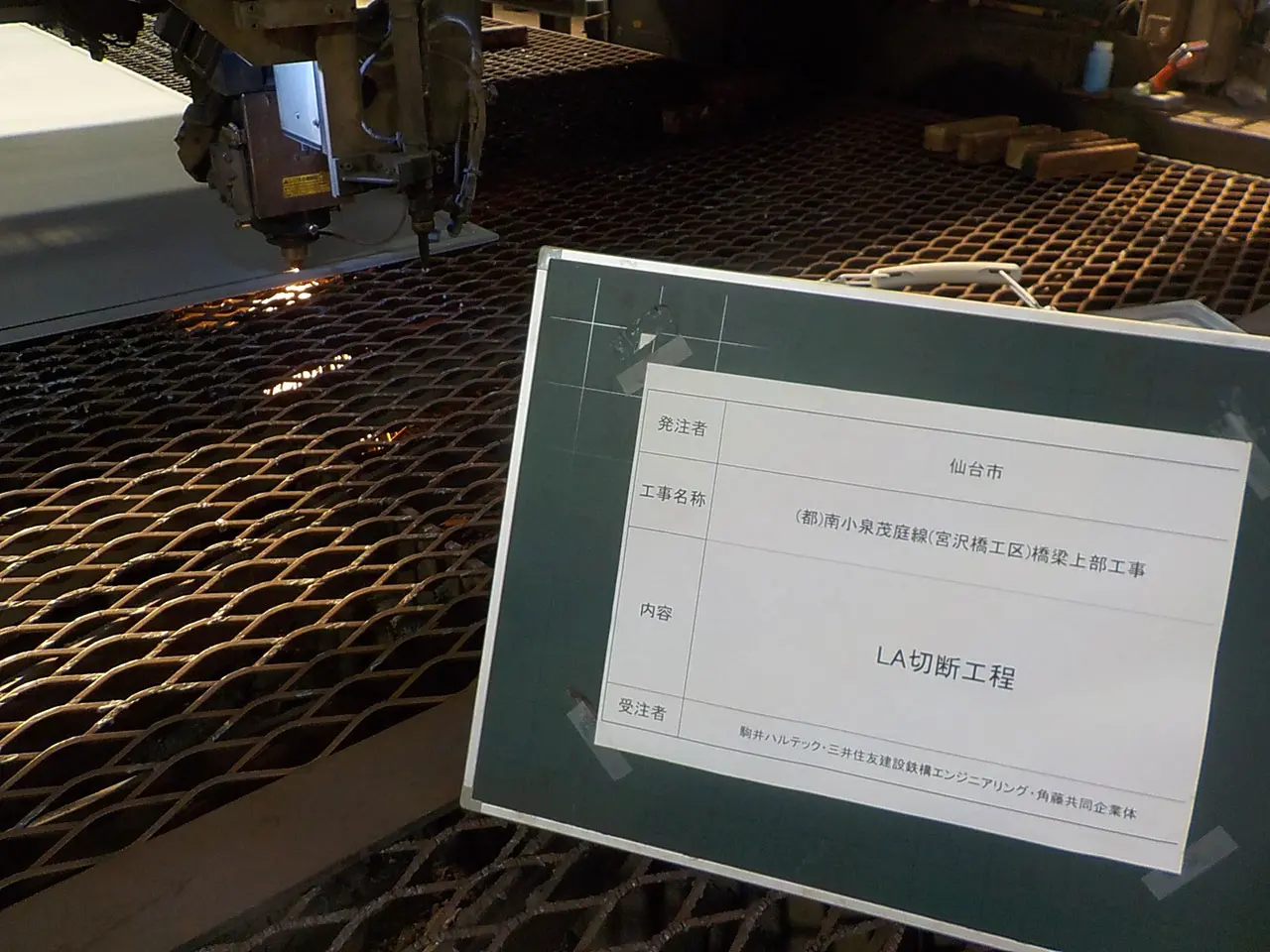
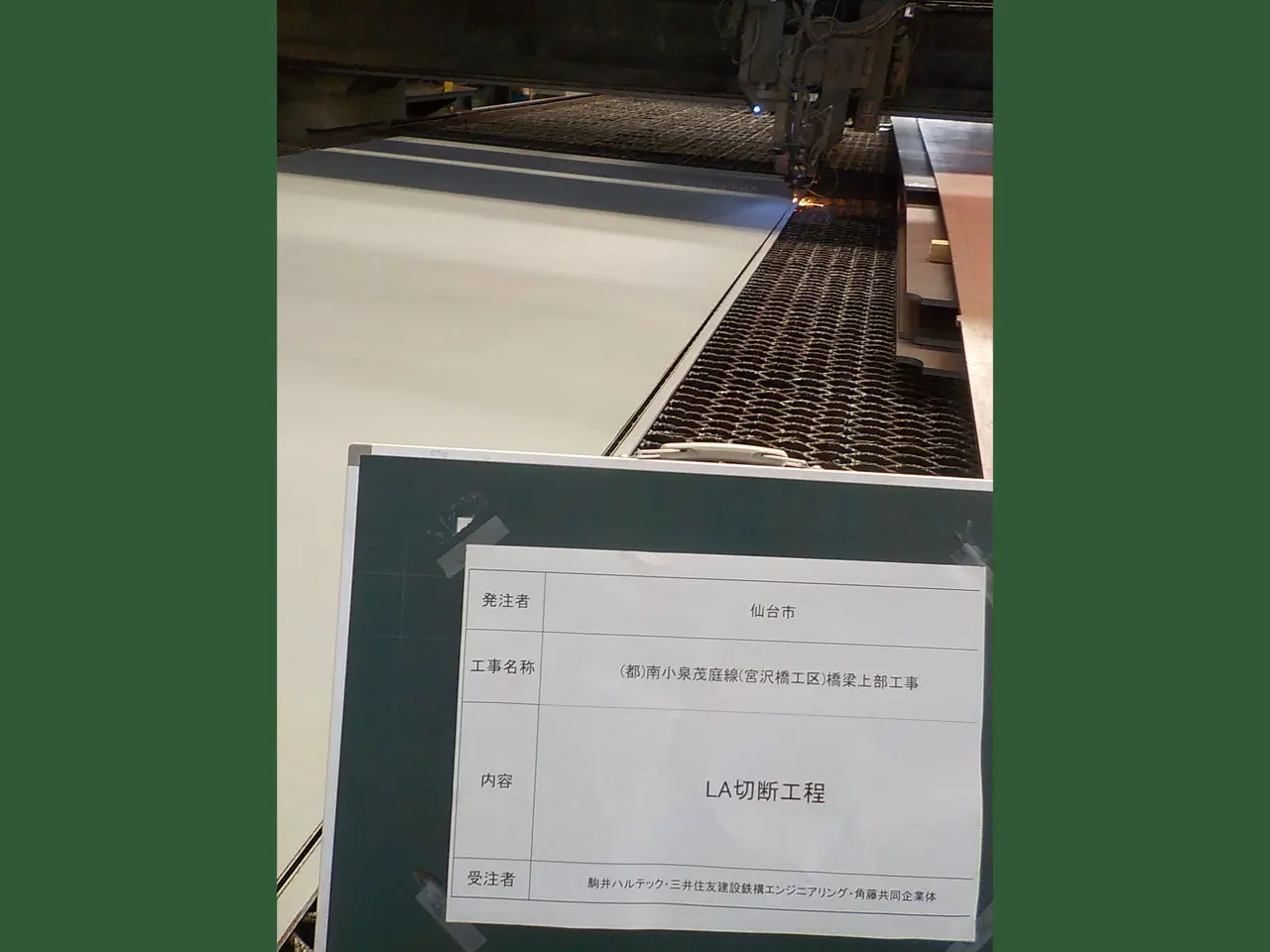
3.切断
材料を原寸作業で決定した寸法に切断します。切断は作業は、使用する材料、板厚によって切断機器を変更します。
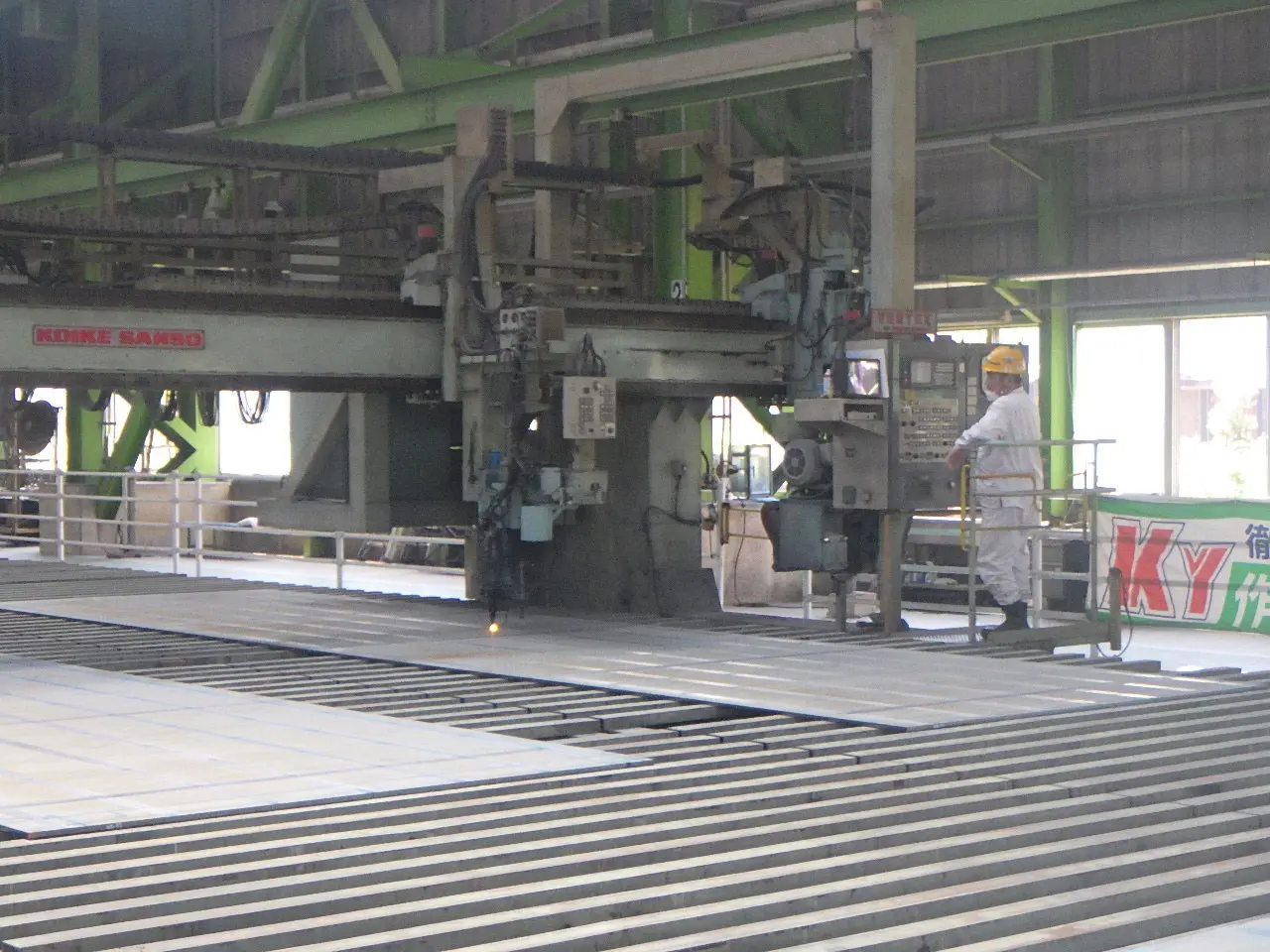
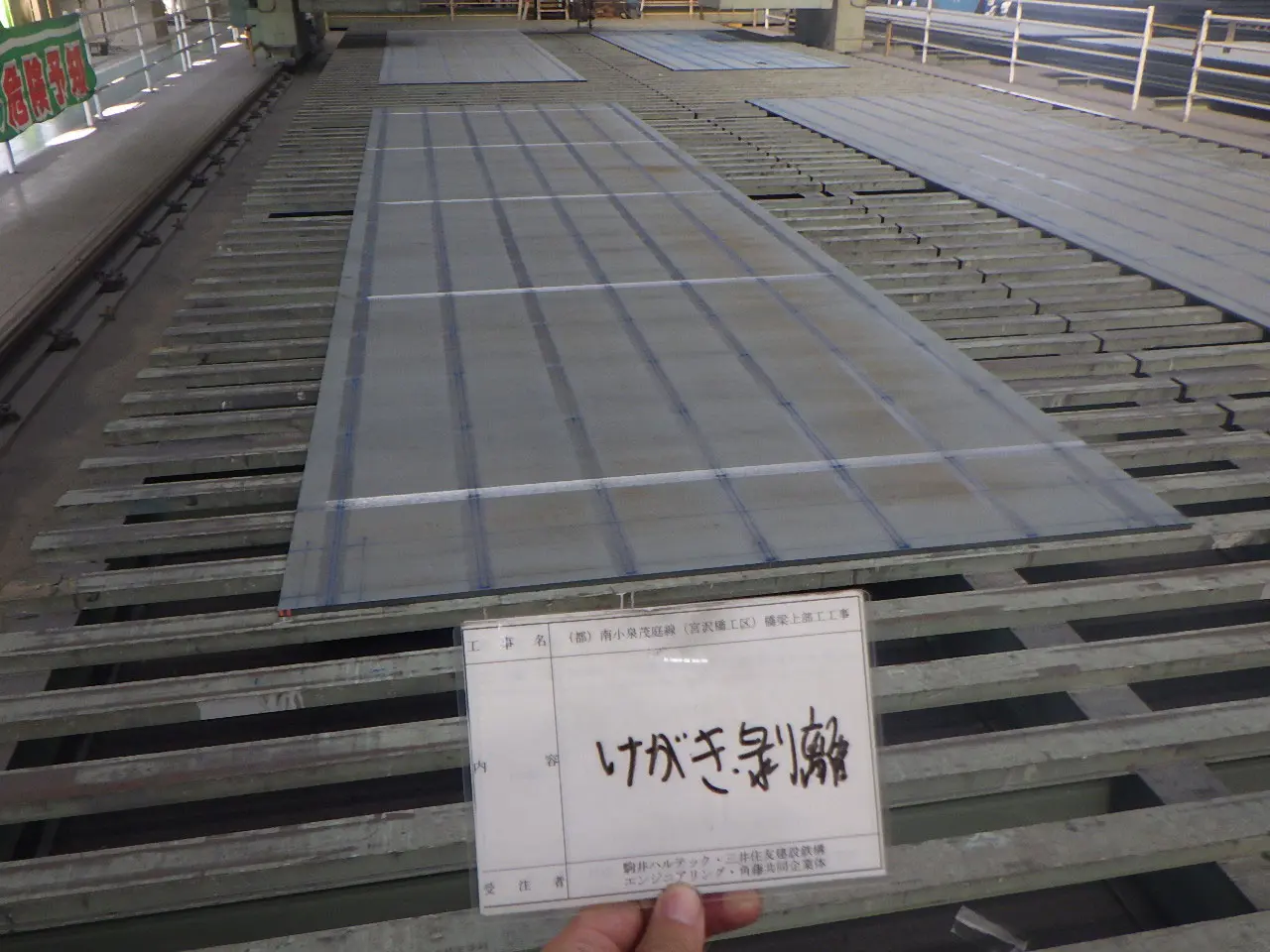
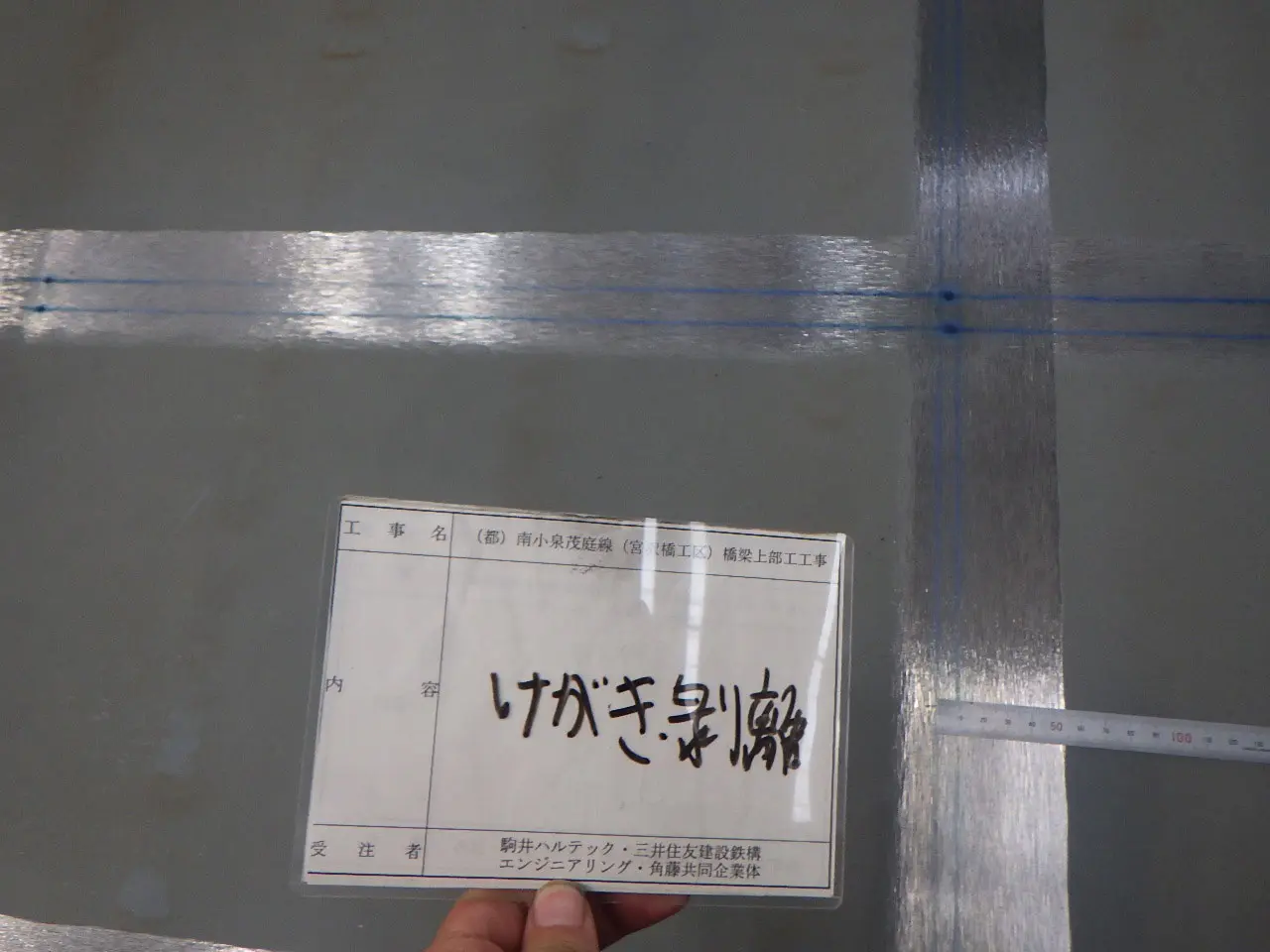
4.罫書き
けがき作業とは、原寸作業により得られた、定規、型板、NCデータを用いて鋼材表面に、切断線、孔位置、部品の取付位置、材片の番号やその他の必要事項を書き込む作業です。
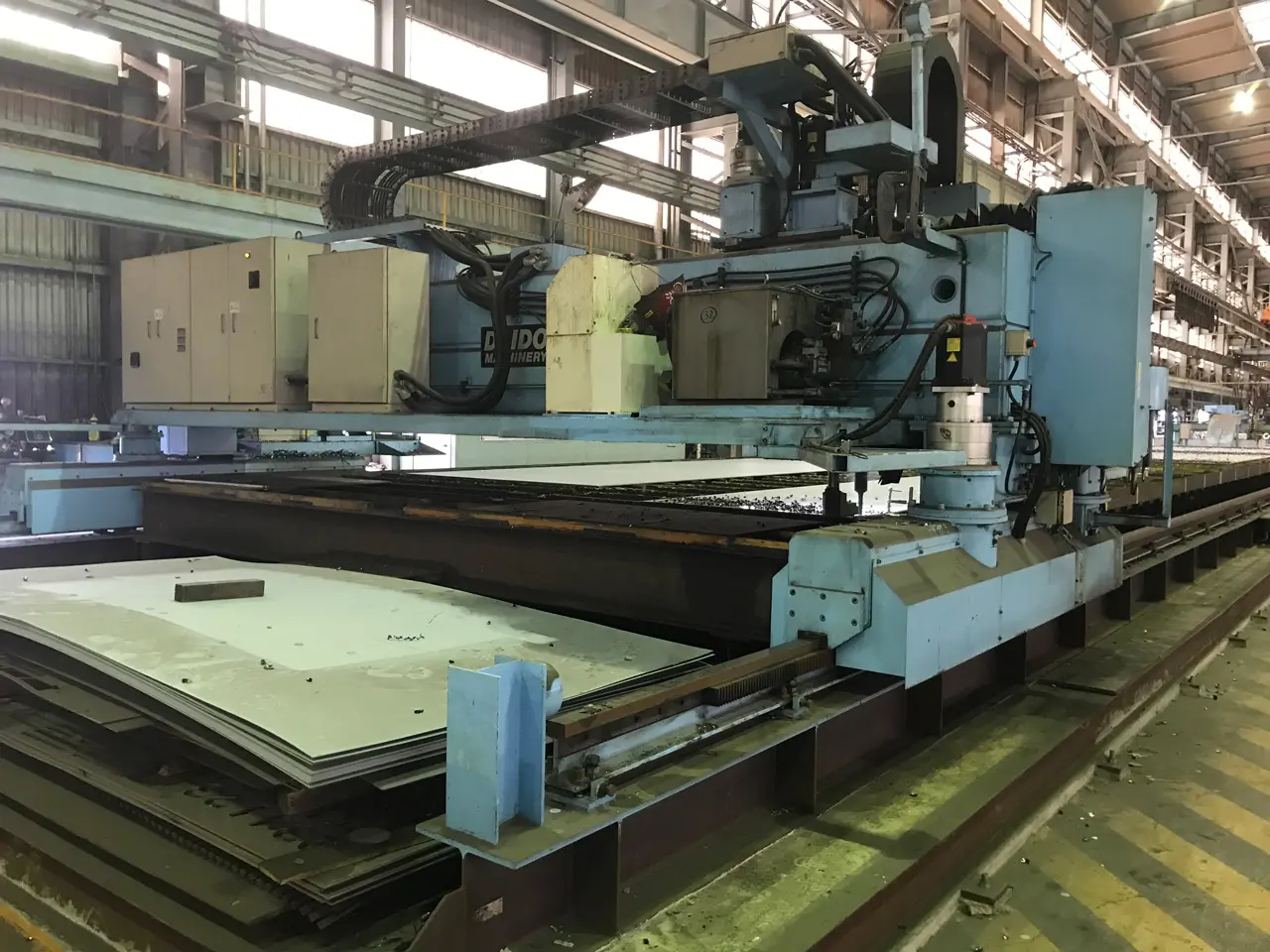
5.孔明け
部材を連結する為の孔等を孔明けします。ボルト孔などの孔明けは、一般的にドリルによるきりもみ方法で行います。
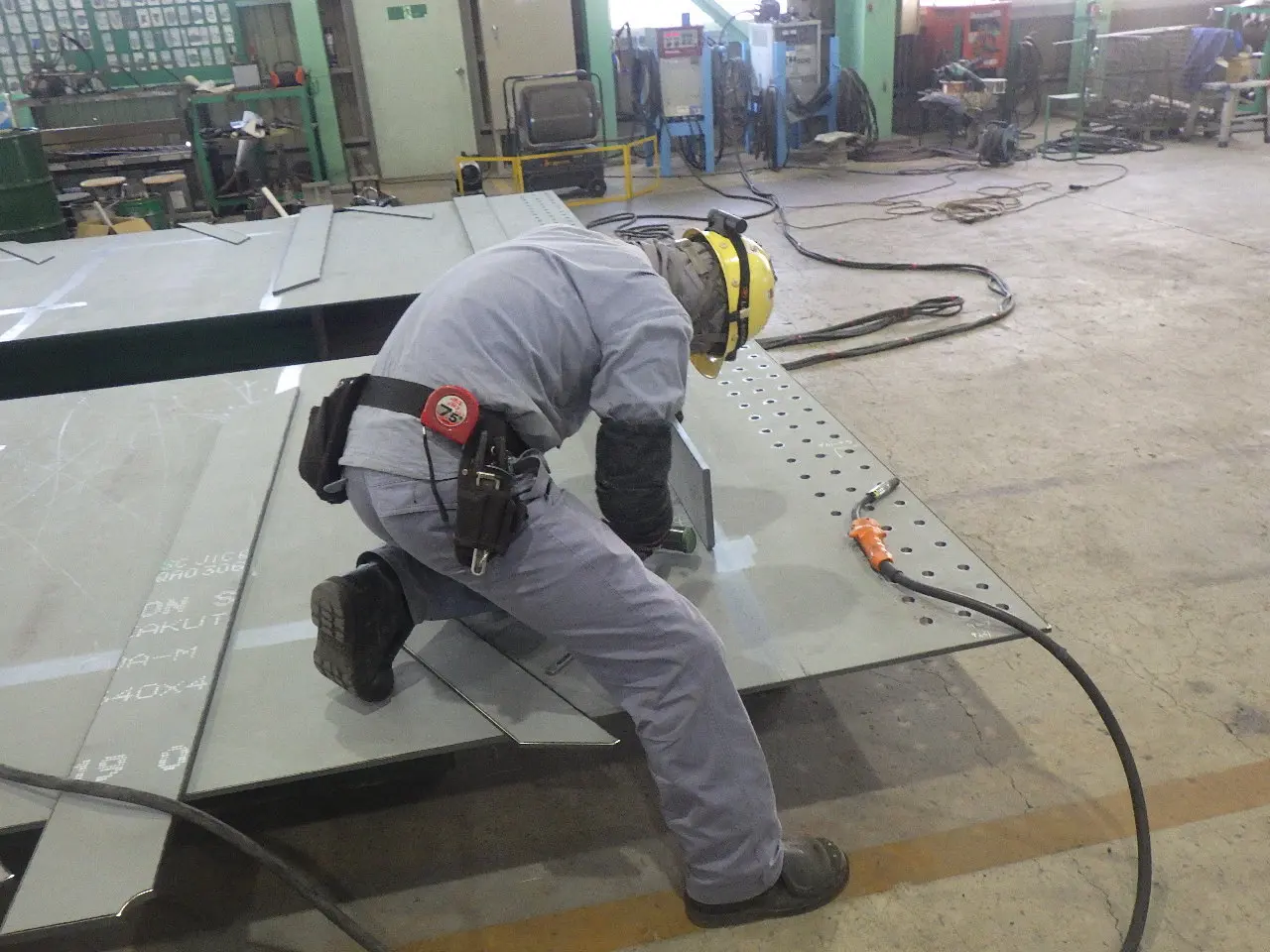
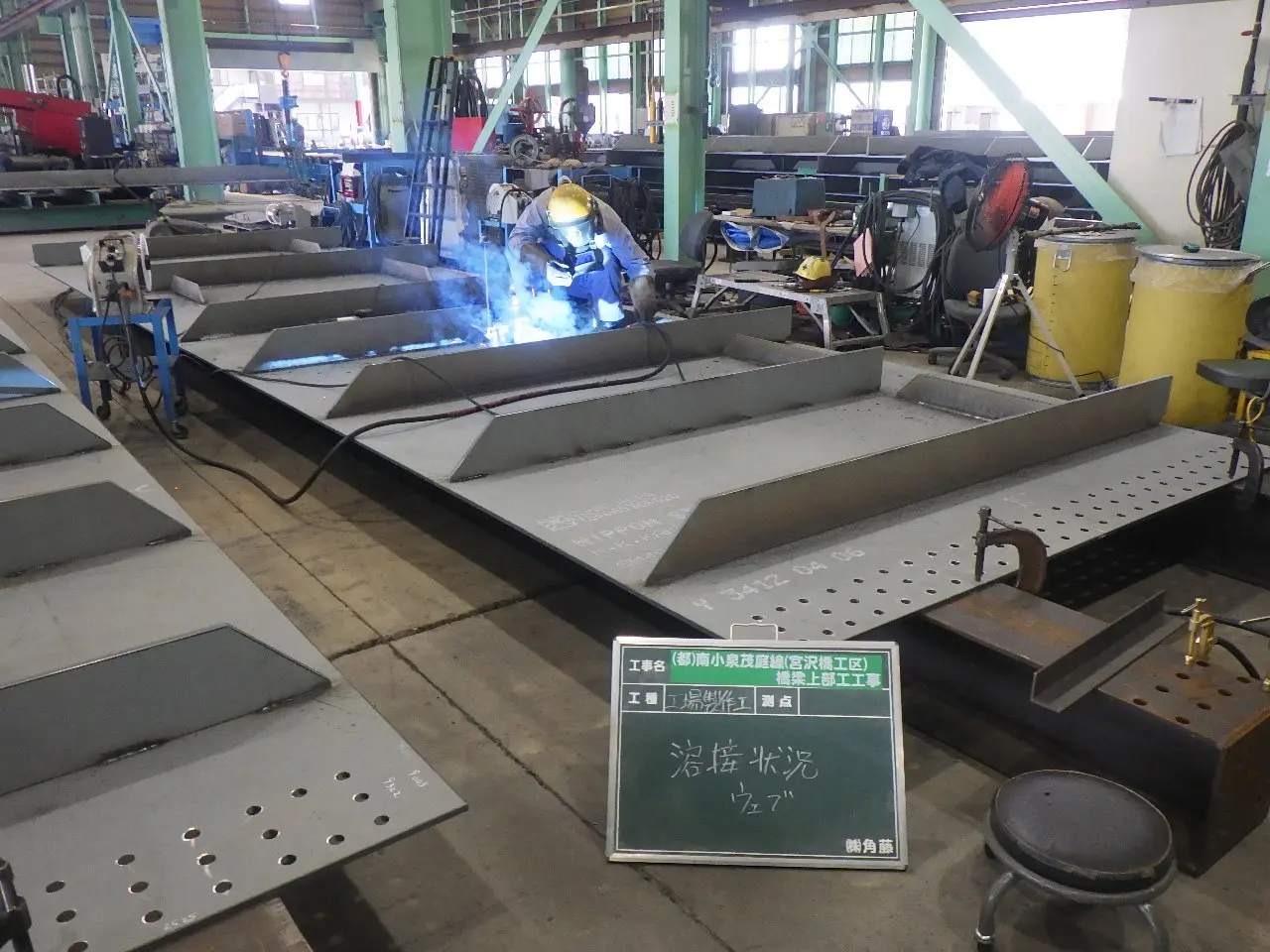
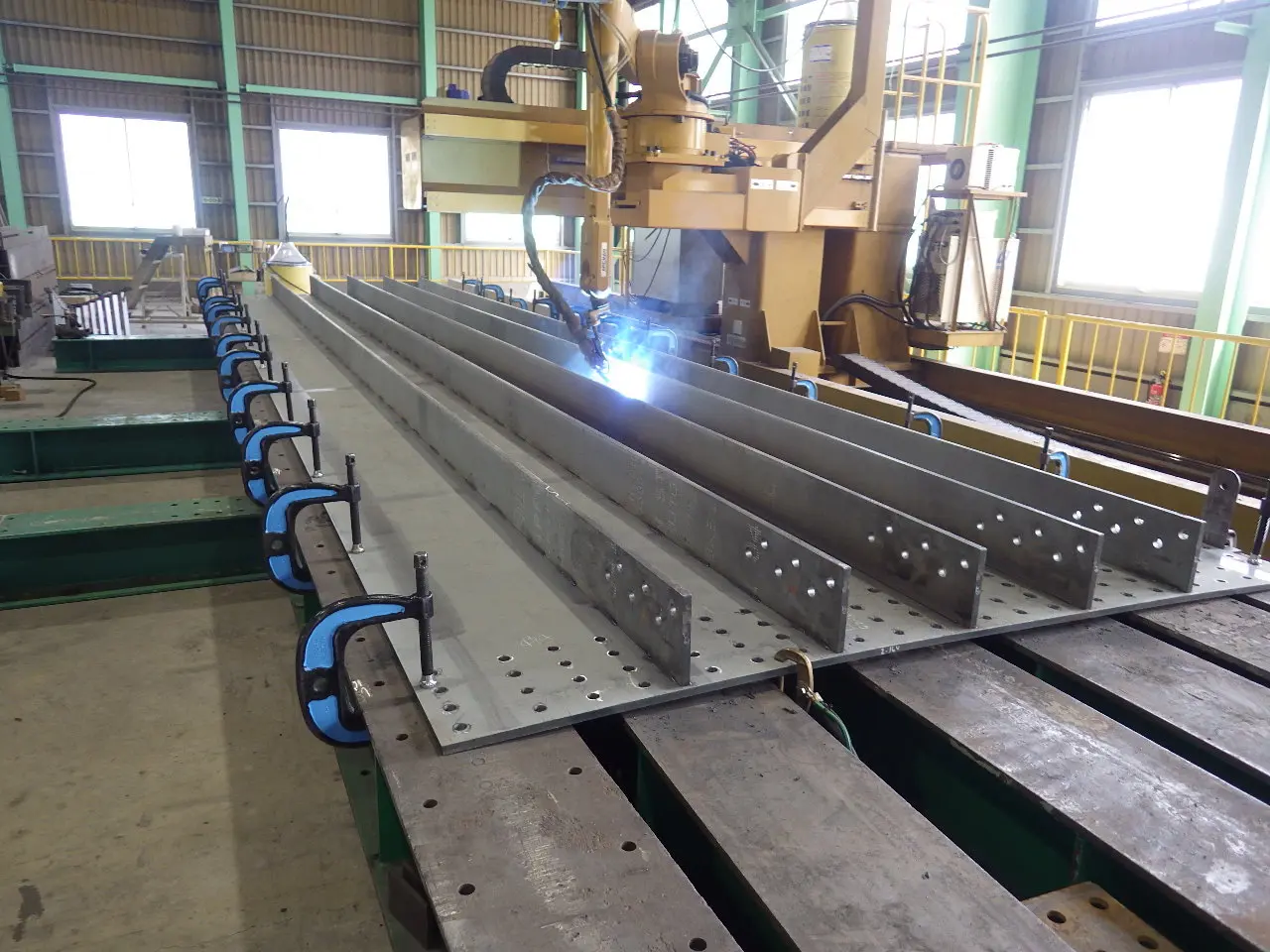
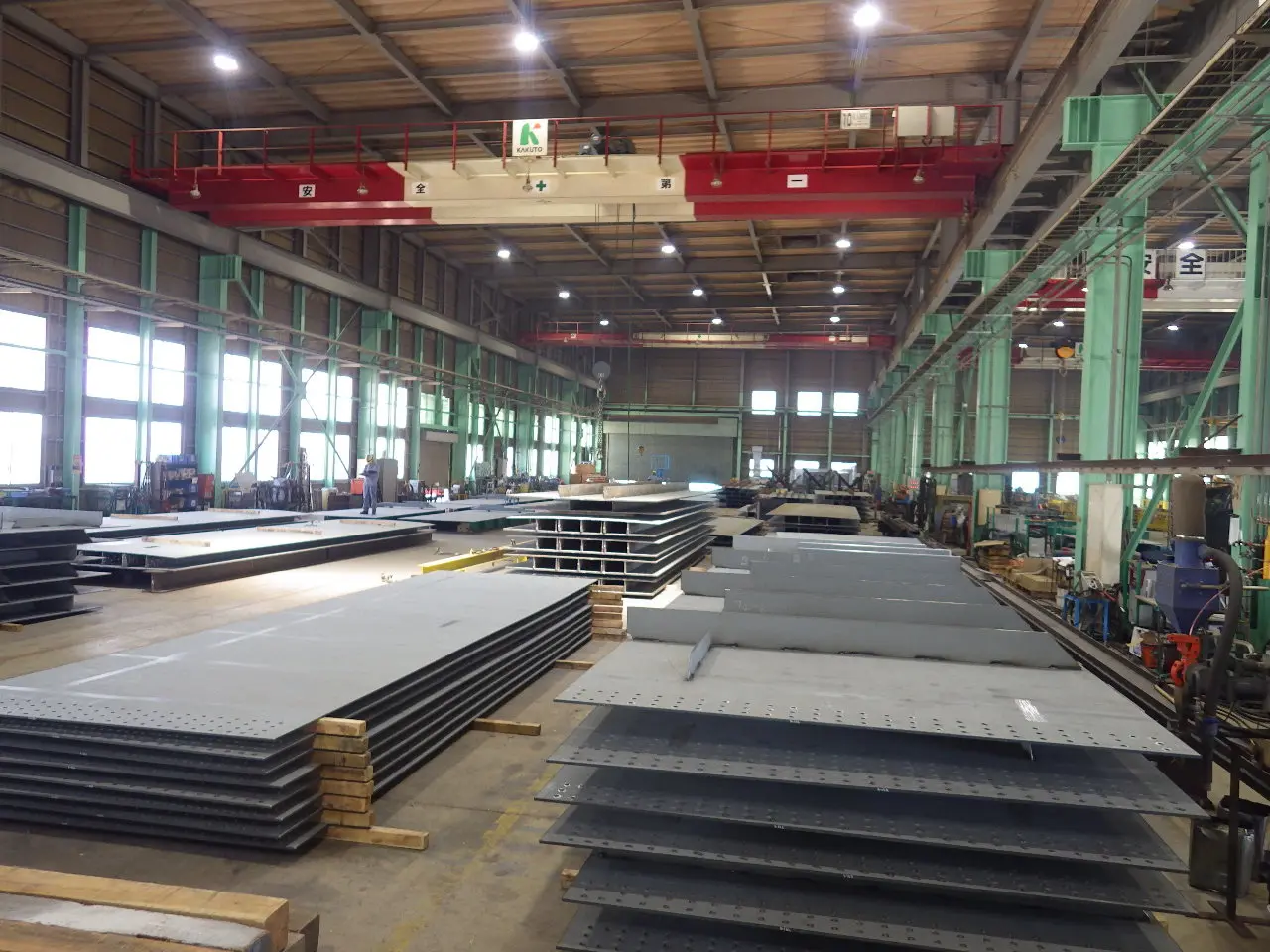
6.パネル組立・溶接
箱桁部材は、主に上・下フランジ、L・RWEB材の4枚のパネルで構成されます。
箱桁形状に組立する前に各部材に取り付く補剛材等の材料を先行で組立・溶接します。
先行で組立・溶接を行う事で、自動機器での施工を行う事が可能となります。
箱桁形状に組立する前に各部材に取り付く補剛材等の材料を先行で組立・溶接します。
先行で組立・溶接を行う事で、自動機器での施工を行う事が可能となります。
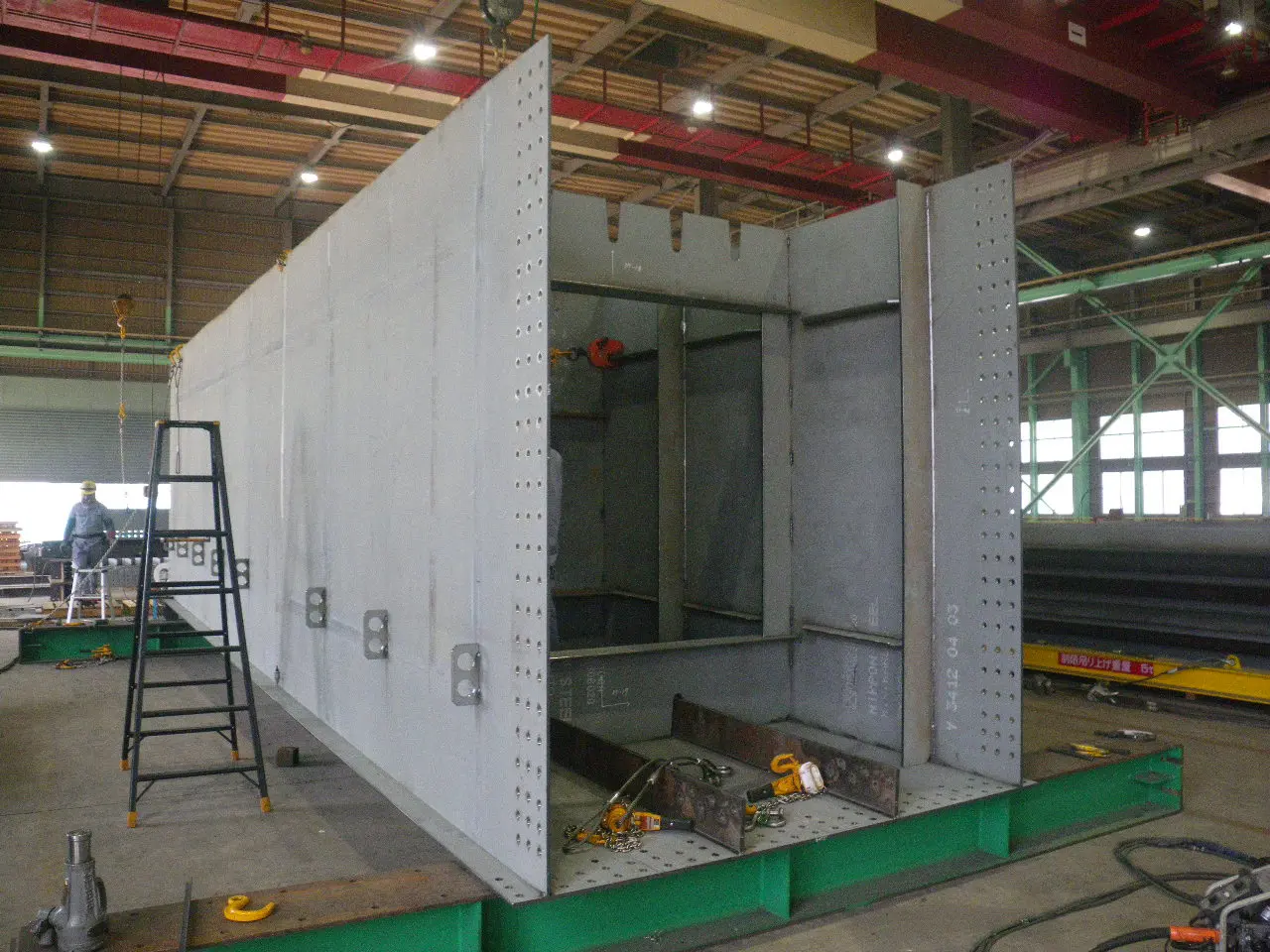
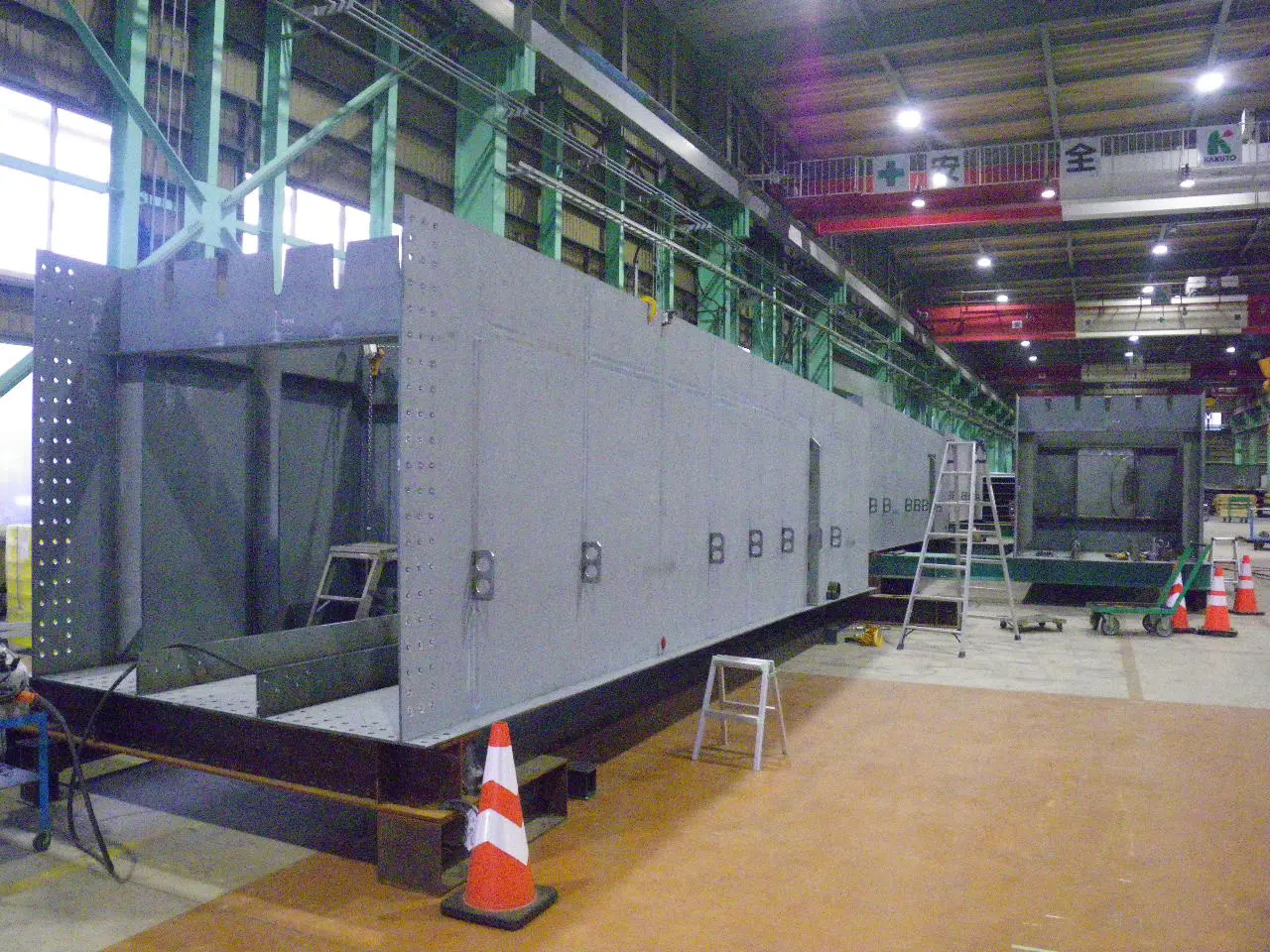
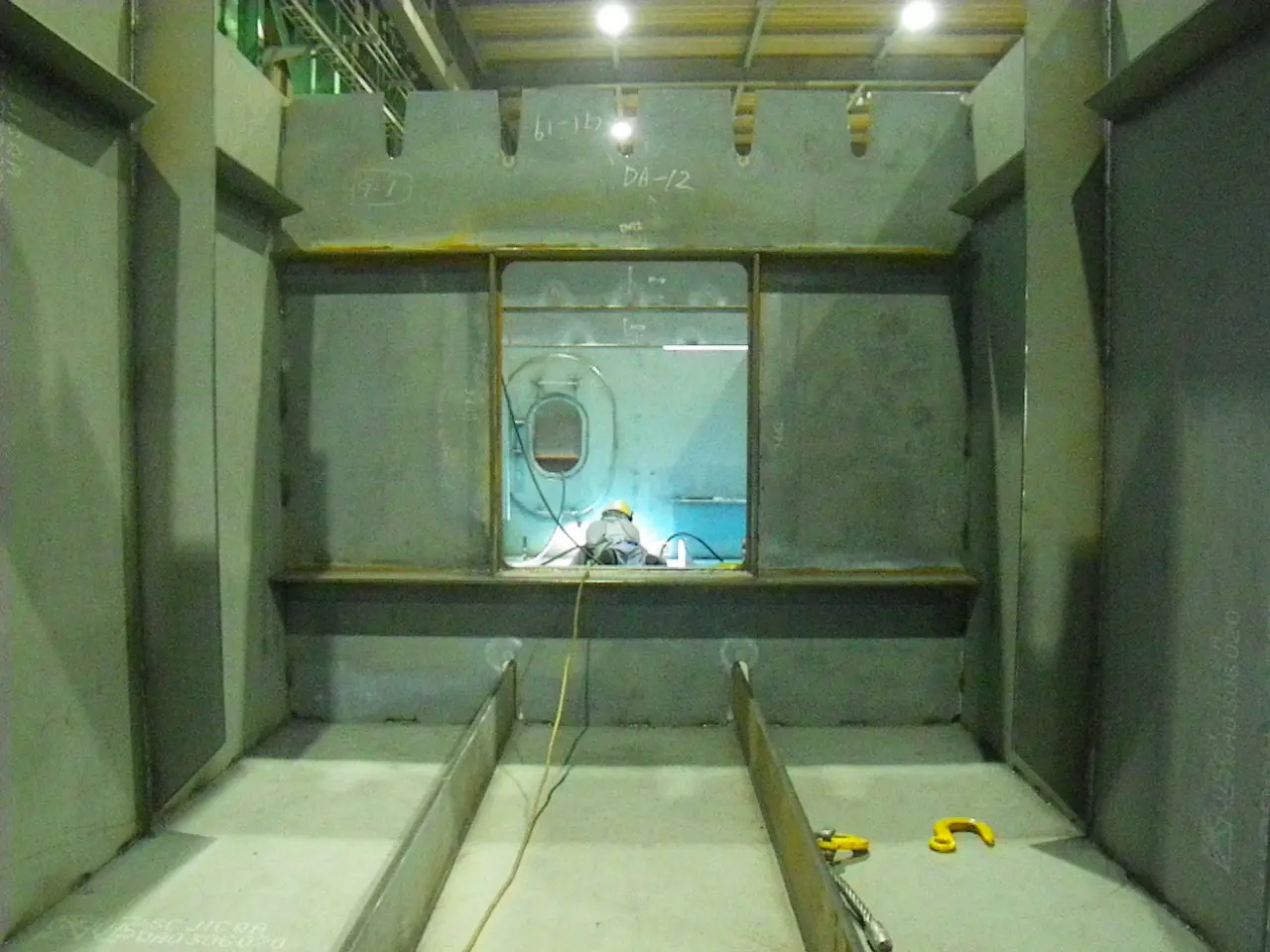
7.大組立
先行溶接したパネルを箱形状に組立てます。
- まず、上フランジパネルを下にして横リブ・ダイヤフラムを組立てます。
- 次に両サイドへウェブパネルを組立てます。
- 最後に、下フランジパネルを組み立てて、箱形状となります。
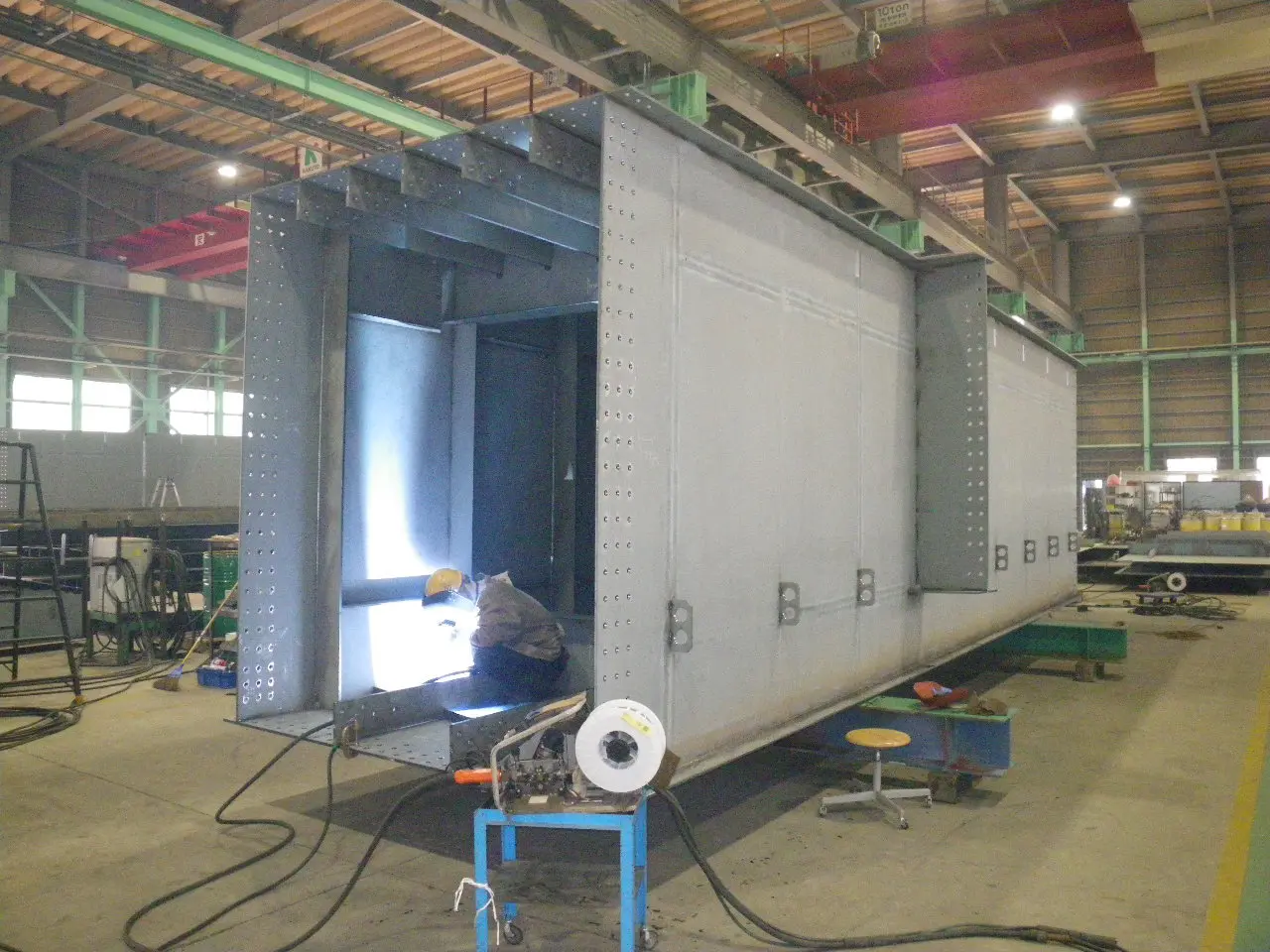
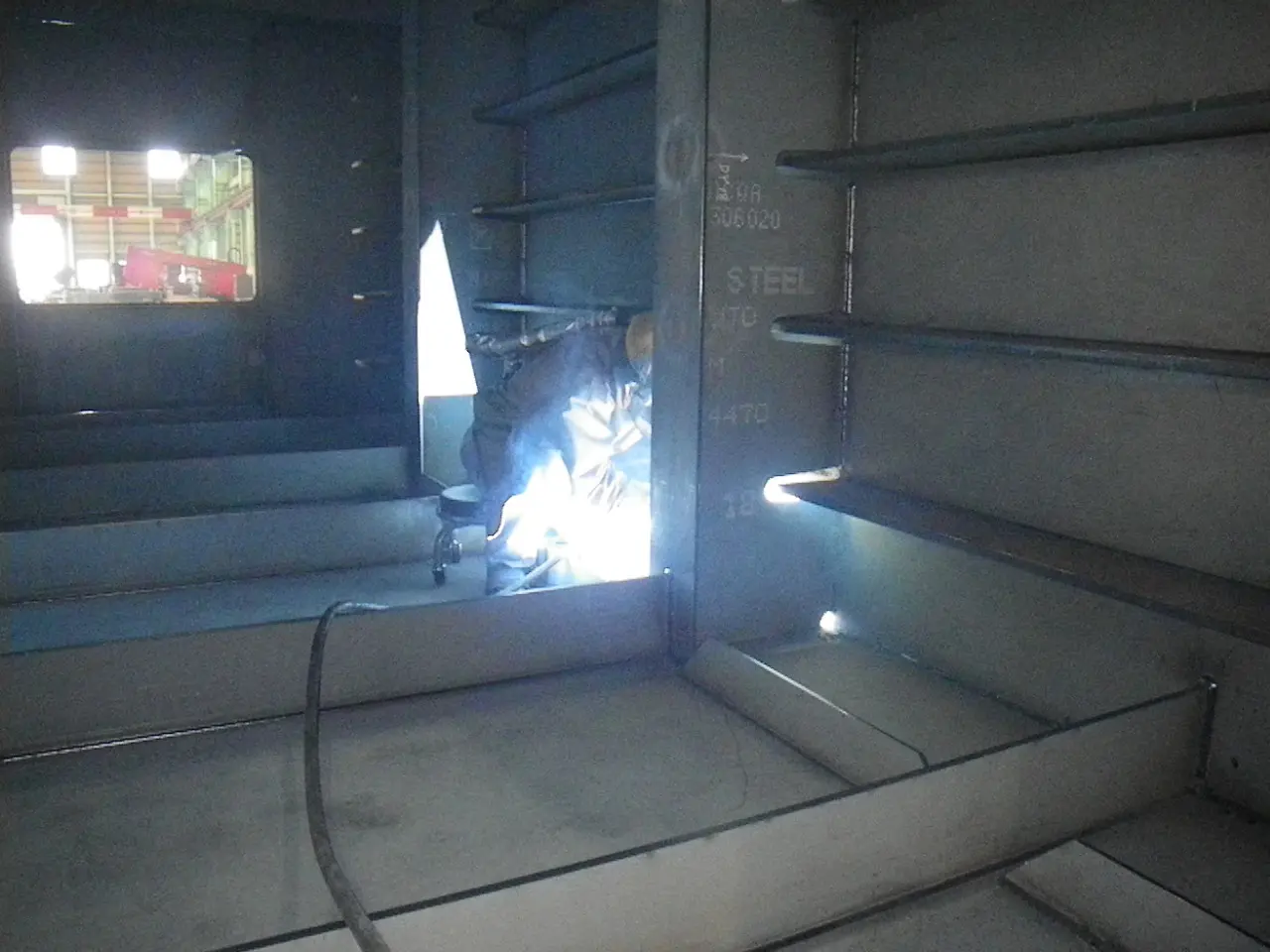
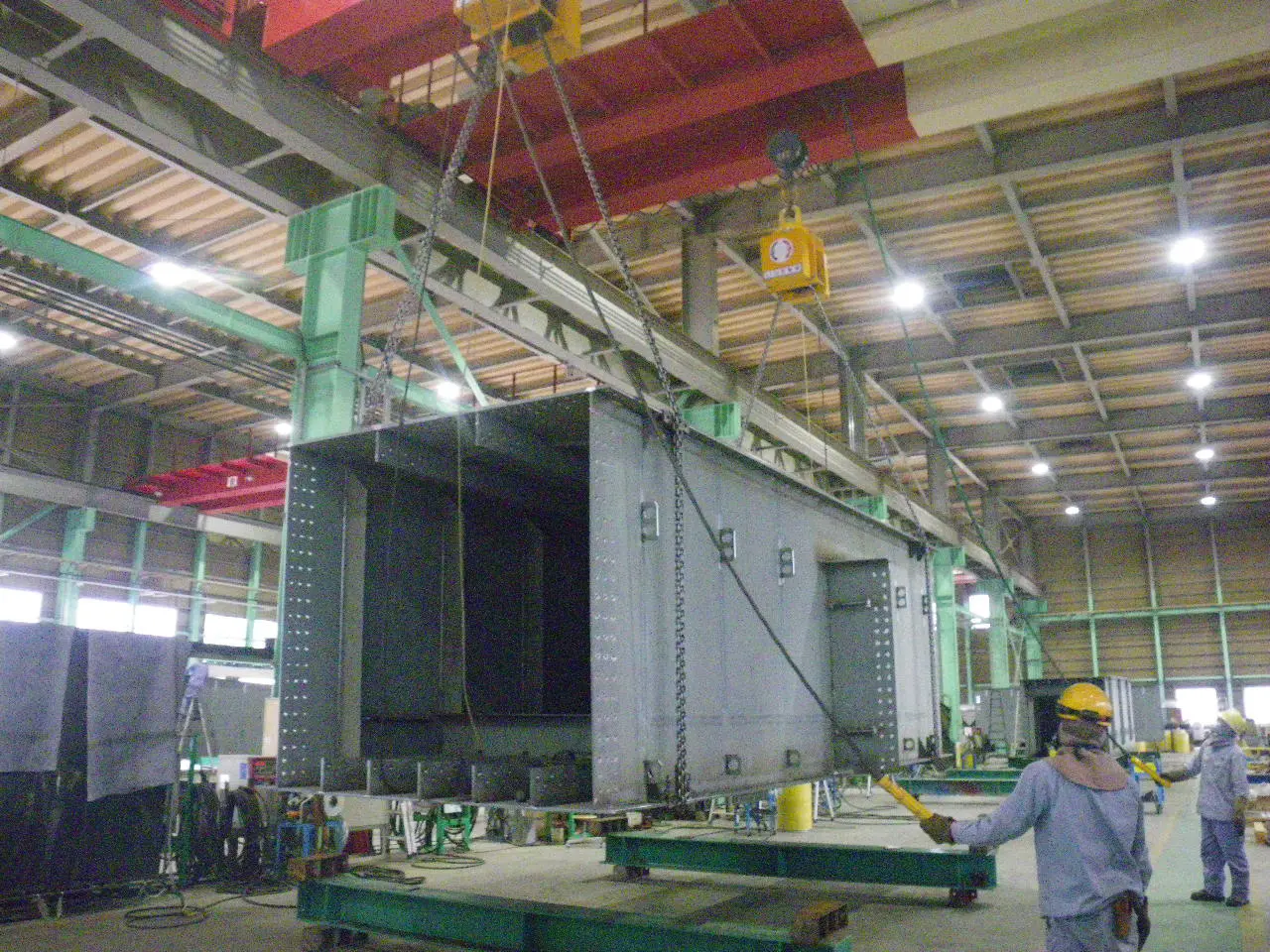
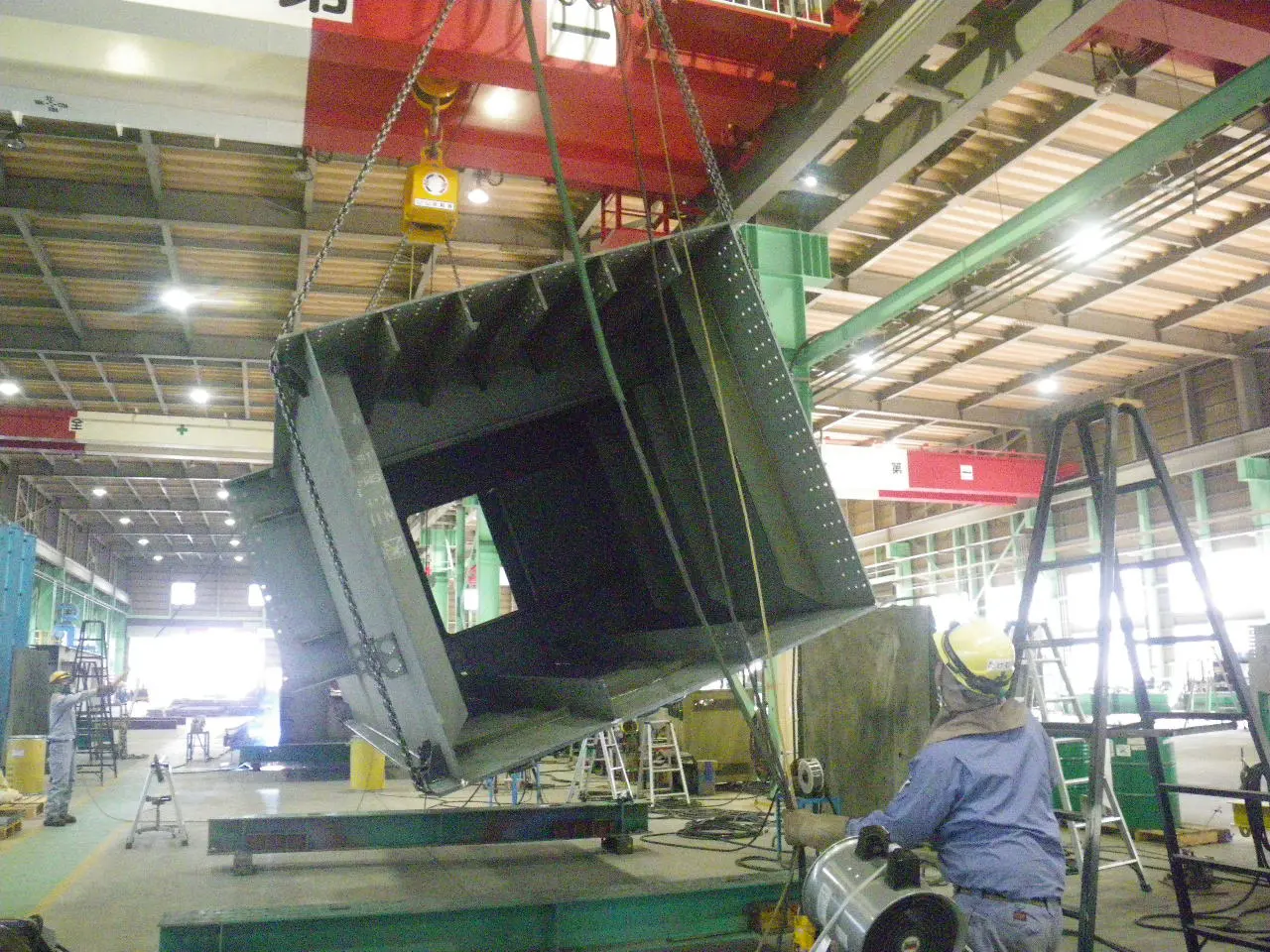
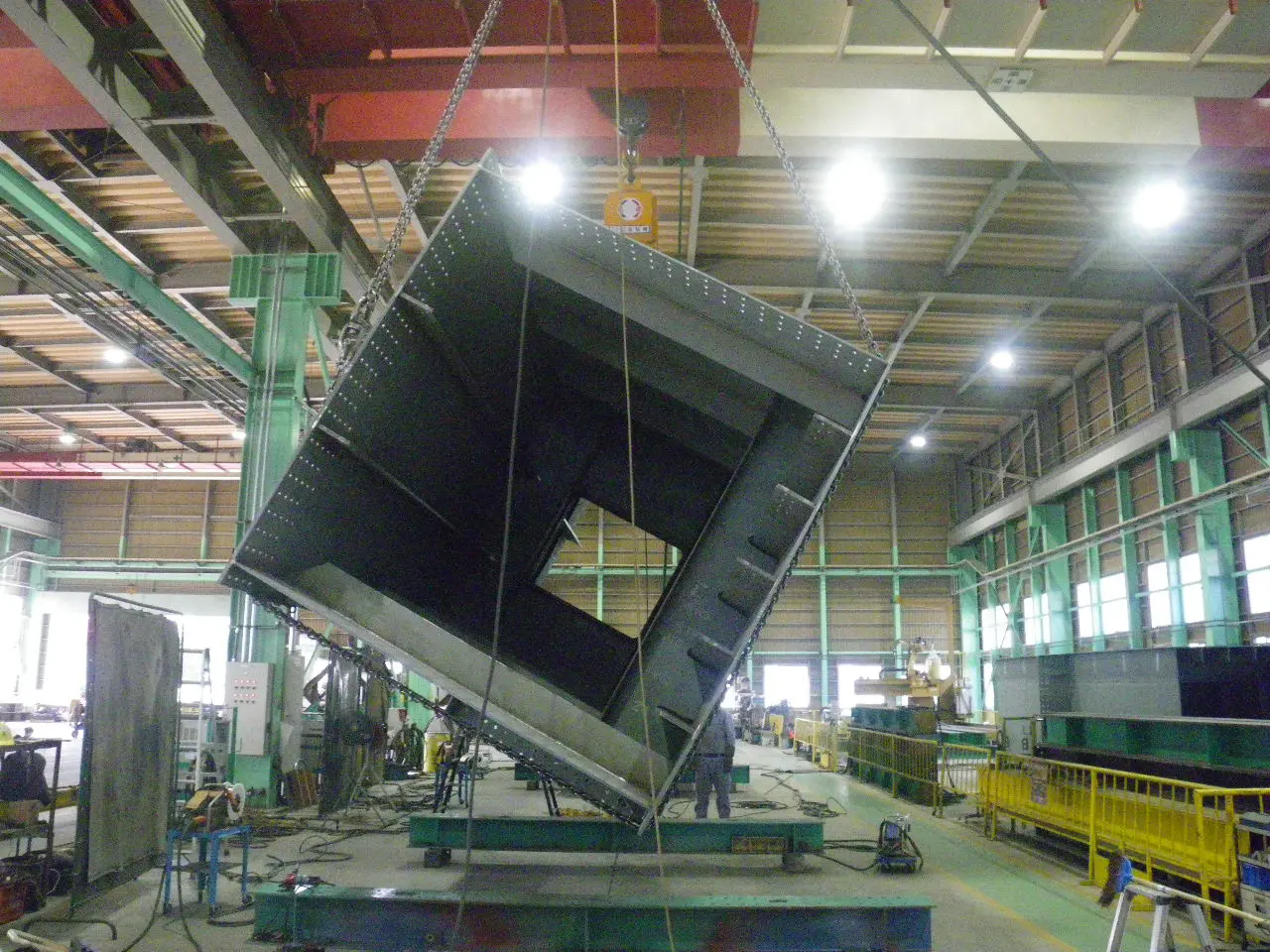
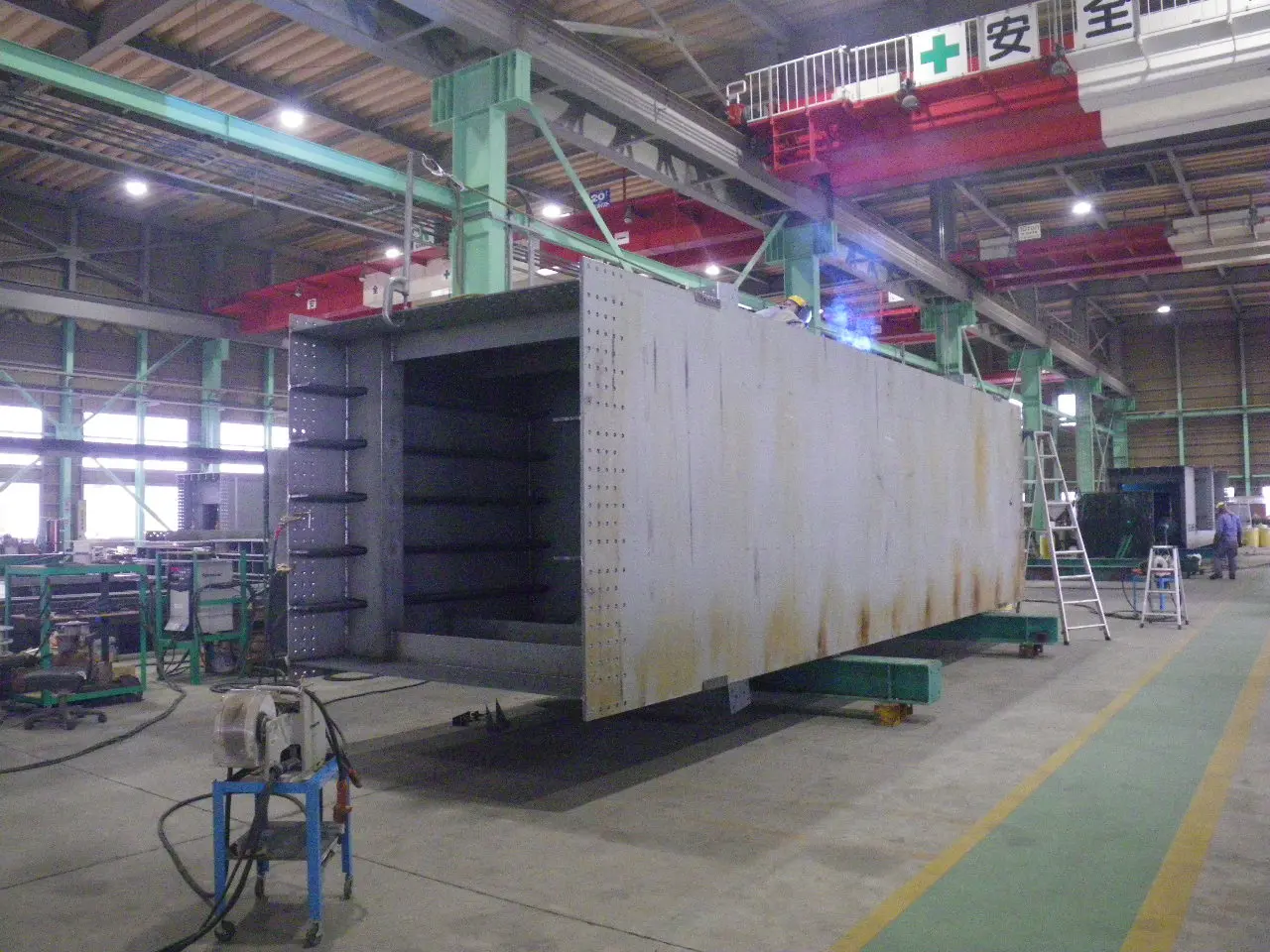
8.大組立溶接
組立てを行った部材を本溶接します。部材は,クレーンを使用し箱桁を回転させながら施工条件の良い下向きで行います。
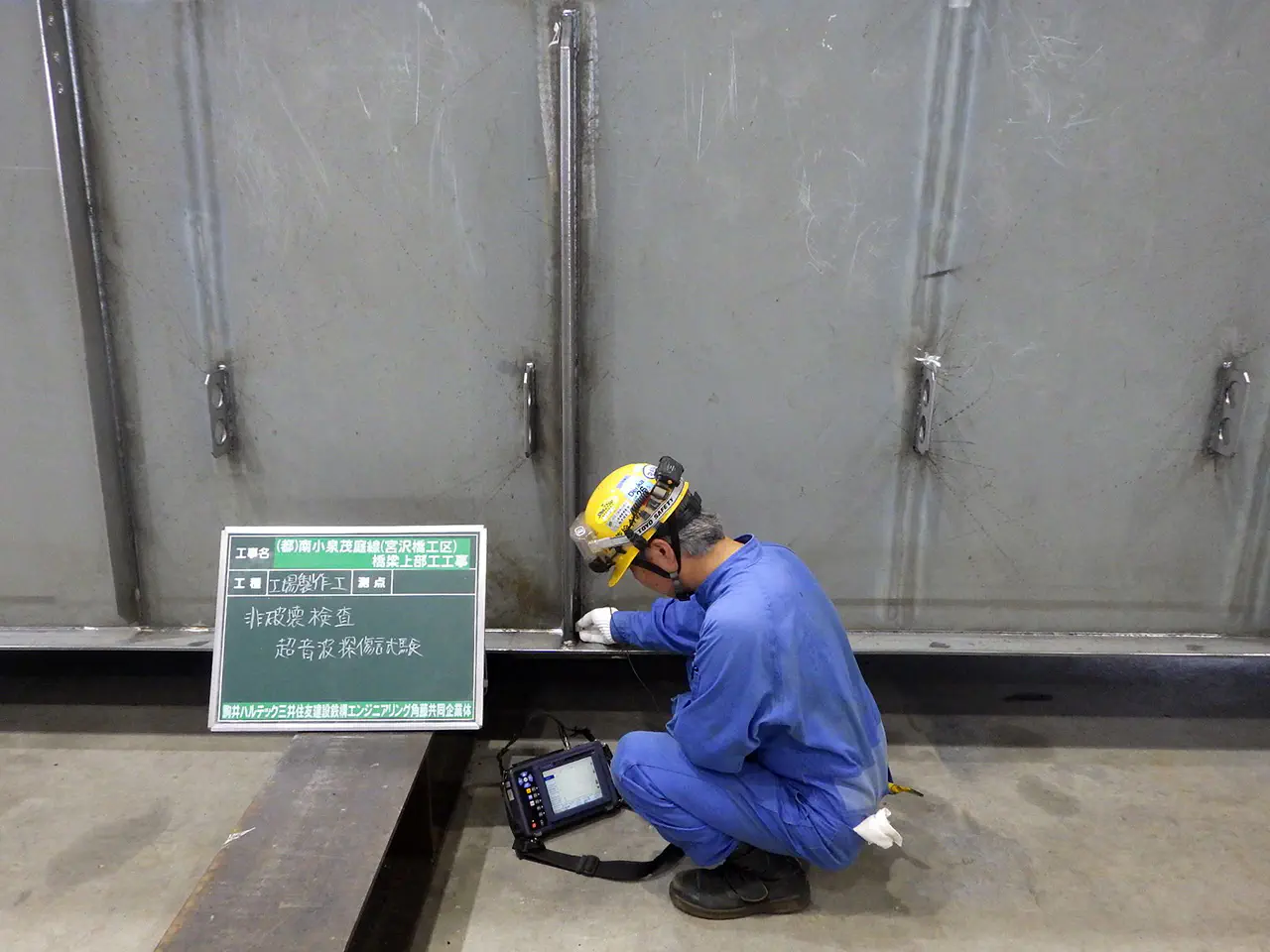
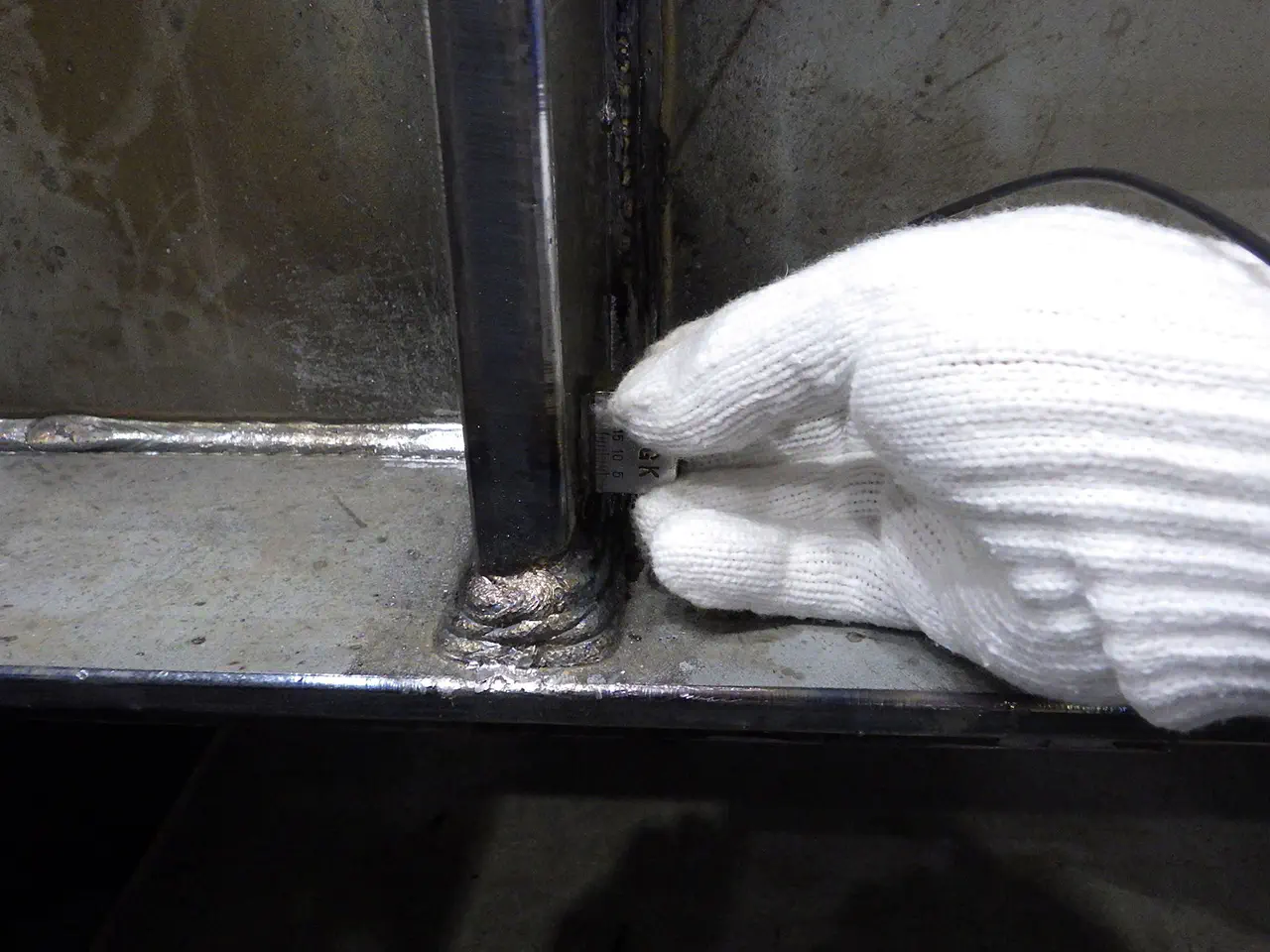
9.非破壊検査(UT)
溶接完了後、非破壊検査にて設計図面に示された箇所の溶接内部の健全性確認を行います。
内部きずの検査方法としては超音波探傷試験を行います。
超音波探傷検査では、溶着金属内部で反射されて戻ってきた超音波が受信されると、内部にきずがあると判断します。
内部きずの検査方法としては超音波探傷試験を行います。
超音波探傷検査では、溶着金属内部で反射されて戻ってきた超音波が受信されると、内部にきずがあると判断します。
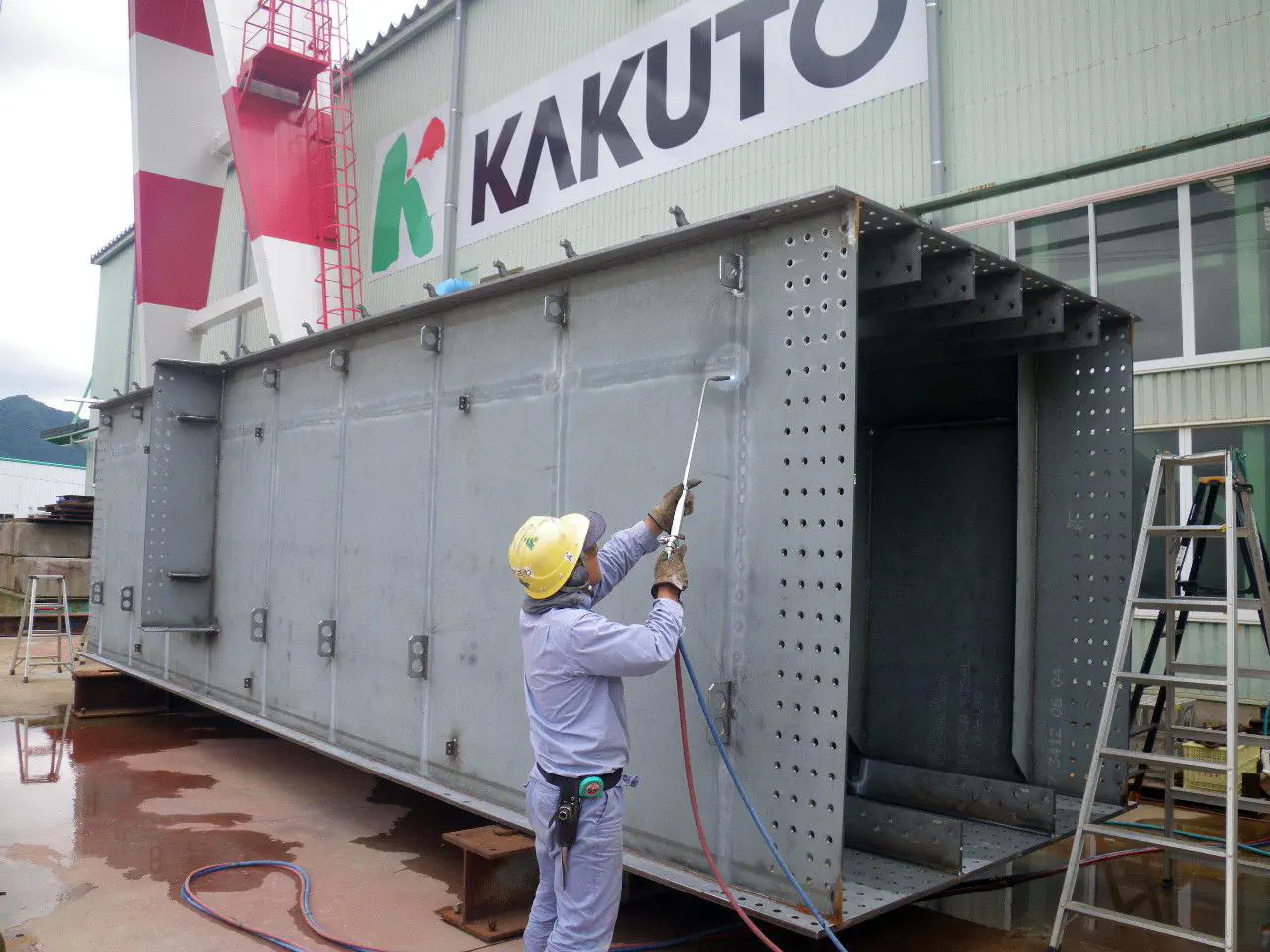
10.歪み矯正
溶接を行う事により部材が、収縮・変形します。変形を修正するため、部材をプレス、加熱矯正を行います。
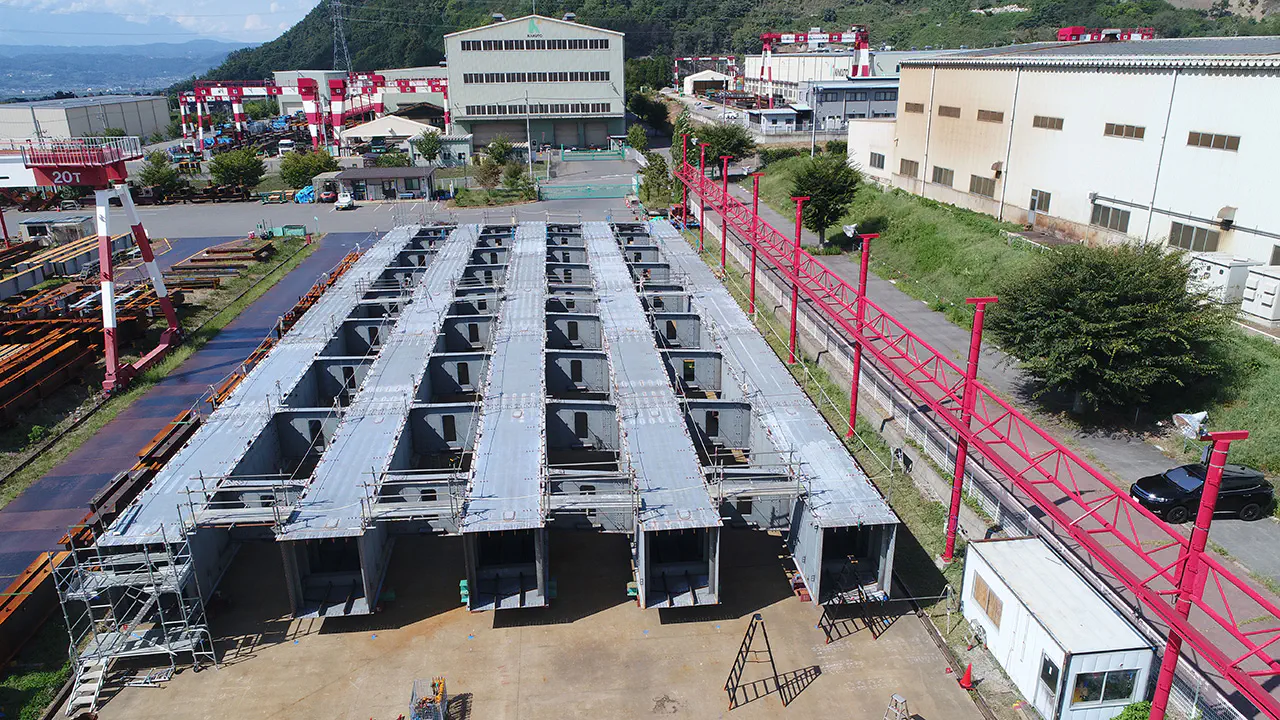
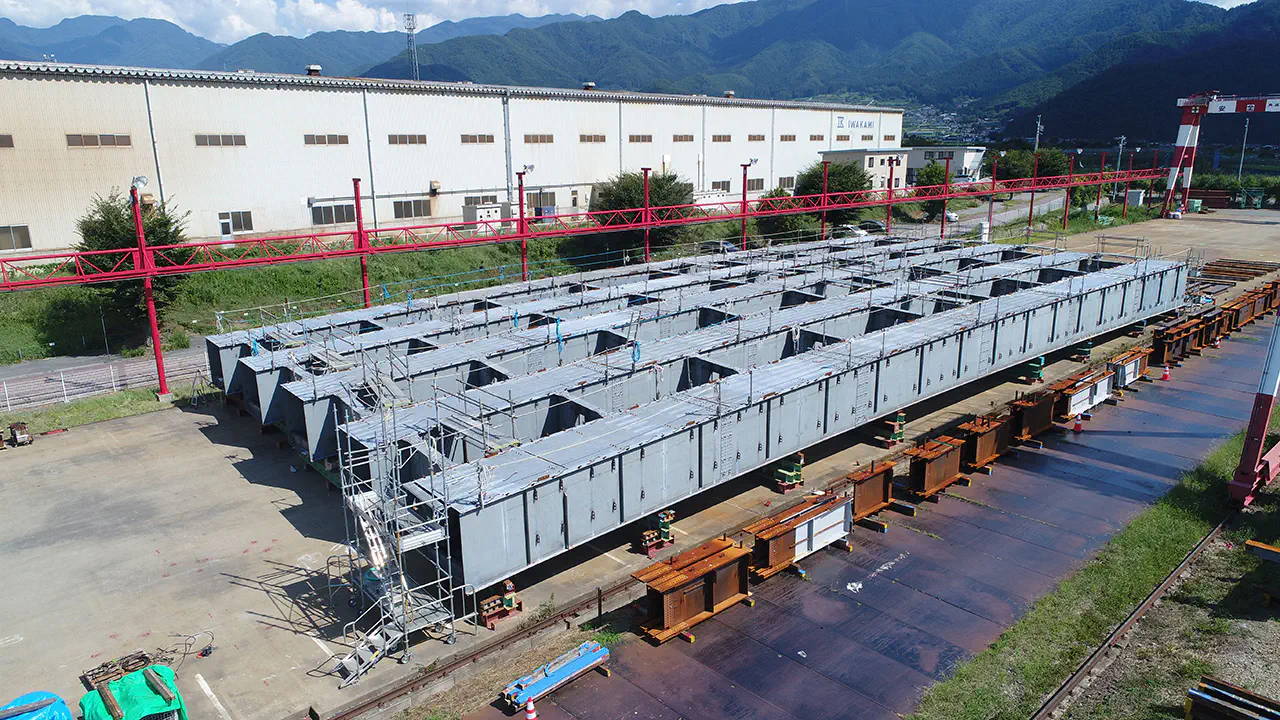
11.仮組立
部材を現場に出荷する前に、工場で連結し、現場に出荷しても問題が無いことを確認します。
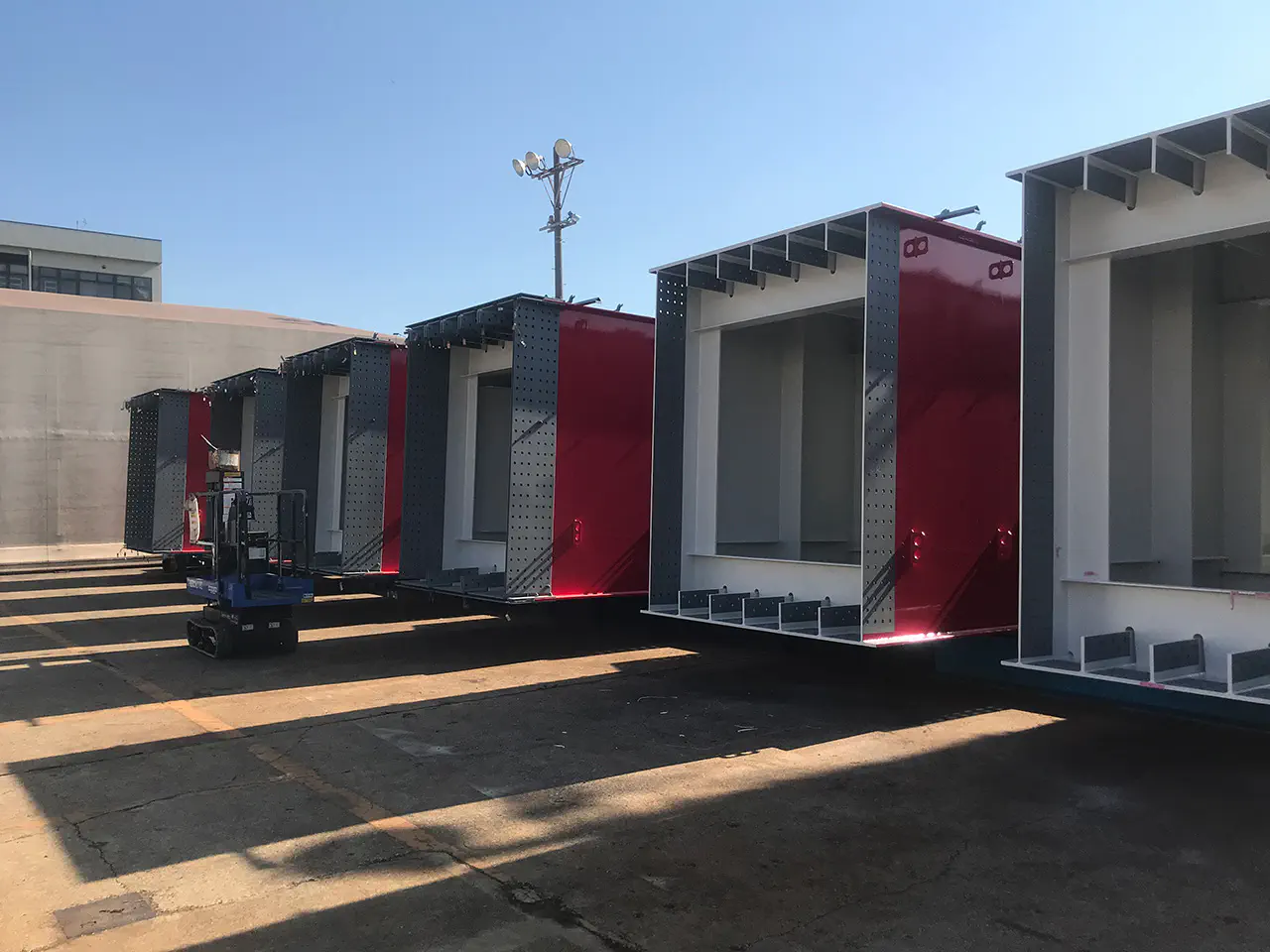
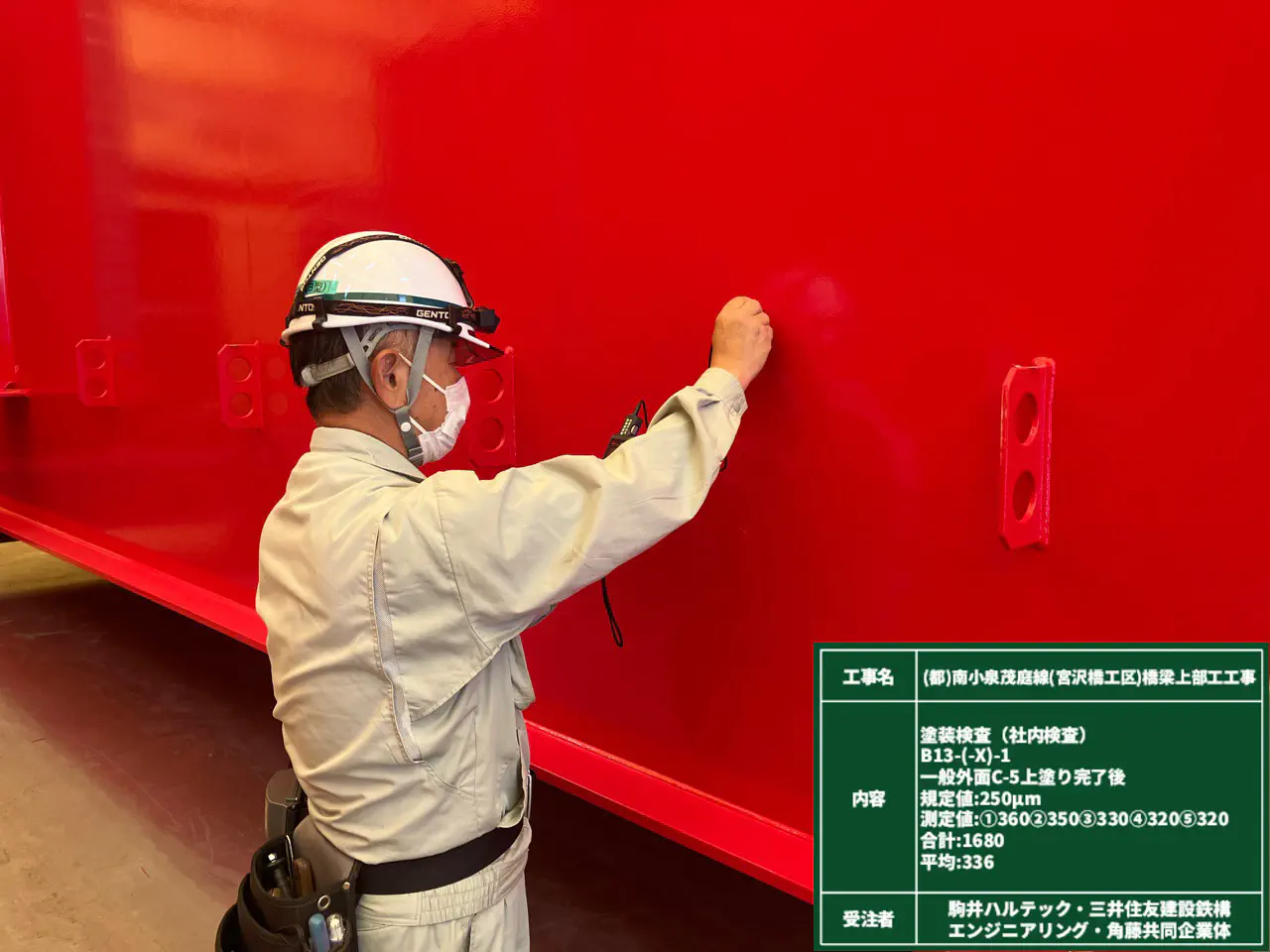
12.工場塗装
鋼橋を長期的に活用出来る用に、塗装を行い保護します。主桁外面部の大半は、機能の異なる塗料を5層塗り重ねる事で、長寿命化を図ります。